مهندسی مکانیک در این تالار مباحث مربوط به مهندسی مکانیک مطرح میشود |

06-06-2014
|
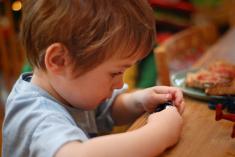 |
مدیر بخش مکانیک - ویندوز و رفع اشکال  
|
|
تاریخ عضویت: Sep 2009
نوشته ها: 2,586
سپاسها: : 5,427
6,159 سپاس در 1,794 نوشته ایشان در یکماه اخیر
|
|
ریخته گری
آشنایی با فرایند ریخته گری
ریخته گری یکی از مهمترین فرآیند های تولید است ، به طوری که مثلا در ایالات متحده آمریکا که یک کشور توسعه یافته صنعتی می باشد، ریخته گری از نظر حجم در مقام ششم صنایع اساسی قرار دارد. یک موتور ۸ سیلندر اتومبیل ممکن است تا حدود ۱۳۰ قطعه ریخته گری داشته باشد. قطعات ریخته گری (ریختگی) از نظر اندازه از حدود ۱ میلیمتر با وزن کمتر از ۱ گرم مانند دندانه یک زیپ لباس شروع و ممکن است تا حدود ۱۰ متر با وزن چندین تن، مانند قطعات کشتی های بزرگ اقیانوس پیما برسد .
در فرآیند ریخته گری اگر قطعه حاصل از تولید به شکل نهایی باشد آن را قطعه ریختگی (Casting) و اگر به شکل واسطه باشد که بعدا به شکلها و مقاطع مختلف تبدیل شود آن را شمش (Ingot) می نامند.
ریخته گری اساسا به فرآیندی گفته می شود که طی آن ماده مذاب ( معمولا یک فلز مذاب) در فضای خالی قالبی که قبلا تهیه شده ریخته می شود ، تا پس از انجماد شکل نهایی قالب را به خود بگیرد. امتیاز مهم ریخته گری در امکان تهیه اشکال پیچیده، قطعات با سطوح منحنی نامنظم، قطعات خیلی بزرگ و قطعاتی که امکان ماشینکاری آنها دشوار است، می باشد.امروزه تقریبا تمام فلزات را می توان ریخته گری کرد، اما این نکته همیشه باید مد نظر باشد که از هر فرآیند شکل دهی زمانی استفاده می کنیم که در مقایسه با روشهای دیگرمقرون به صرفه بوده و دسترسی به تجهیزات و لوازم آن آسان باشد. البته هر فرایند شکل دهی مواد از عواملی نظیرتعداد ، اندازه، کاربرد قطعه و توجیه فنی و اقتصادی تاثیر پذیر خواهد بود.
فلزاتی که غالبا در ریخته گری مورد استفاده قرار می گیرند عبارتند از: آهن، فولاد، آلومینیم، برنج، برنز، منگنز و بعضی از آلیاژهای روی. در میان این فلزات آهن از نظر خواص مطلوب ریخته گری از قبیل سیالیت در حالت مذاب، انقباض نا چیز بعد از سرد شدن ، استحکام کافی و موارد کاربرد ، بیش از سایر فلزات به روش ریخته گری شکل داده می شود. در حالیکه فلزات دیگری از قبیل آلومینیوم به علت وزن کمتر و مشخصات مخصوص در بعضی از صنایع از قبیل صنعت خودرو سازی ، به تدریج جای آهن را می گیرد.
عموما مراحل ریخته گری فلزات به شرح زیر است :
۱- طراحی قطعه مورد نظر و تهیه نقشه ریخته گری از آن.
۲- تهیه مدل مناسب قطعه از روی نقشه های ریخته گری.
۳- تهیه مذاب از فلز مورد نظربا آنالیز مطلوب.
۴- تهیه قالب مناسب یا فضای خالی که به شکل قطعه است.
۵- تهیه ماهیچه برای مناطق تو خالی قطعه ریختگی و نصب آن در داخل قالب.
۶- ریختن فلز مذاب به داخل قالب با دما و سرعت مناسب به طوریکه گازهای متصاعد شده بتوانند از داخل قالب خارج شوند و فضای قالب به طور کامل از فلز مذاب پر شود.
۷- کنترل سرد شدن فلز مذاب در داخل قالب به طوری که بر اثر انقباض، فضای خالی یا حفره در داخل قطعه ایجاد نشود.
۸- بعد از انجماد قطعه ریختگی به راحتی باید بتواند از درون قالب بیرون بیاید.
۹- قسمت های اضافی که به قطعه چسبیده اند باید به آسانی از قطعه جدا شوند.
تهیه قالب
تهیه قالب یکی از مهم ترین مراحل ریخته گری فلزات می باشد. توجیه پذیری اقتصادی، تعداد قطعه، اندازه قطعه، کیفیت سطح قطعه، پیچیدگی شکل قطعه از عوامل مهمی هستند که در قالب گیری یا تهیه قالب قطعات ریختگی باید مدنظر قرار بگیرند. امروزه مهمترین روشهای قالب گیری ( تهیه قالب) فلزات به شرح زیر می باشند:
۱- ریخته گری در قالب ماسه ای
۲- ریخته گری در قالب دائمی بدون فشار
۳- ریخته گری در قالب دائمی تحت فشار( دایکاست)
۴- ریخته گری گریز از مرکز که عمدتا در داخل قالب های فلزی صورت می گیرد. گرچه ممکن است در داخل قالب های ماسه ای نیز انجام شود.
۵- ریخته گری بامدل های ذوب شدنی( Lost Wax Casting وLost Foam Casting ) که ریخته گری دقیقی برای قطعات بسیار بزرگ تکی می باشد.
۶- ریخته گری پوسته ای ( Shell Molding )
7- ریخته گری در قالب گچی ( Plaster Molding) که معمولا برای قطعات دقیق و زینتی به کار می رود که از آلیاژهایی که نقطه ذوب پائینی ( کمتر از ۱۰۰۰ درجه سانتیگراد ) دارند، ساخته می شوند.
تهیه مدل
مدل دقیق مشابه قطعه ریختگی می باشد که تغییراتی بر حسب نیاز بر روی آن انجام می شود. مدل های دائمی بر حسب تعداد قطعات ریختگی از چوب، پلاستیکهای فشرده یا آلومینیم ساخته می شوند.
در ساخت مدل پارامترهایی باید مد نظر قرار بگیرند که عبارتند از:
۱- اعمال ضریب انقباض فلز
۲- شیب مدل
۳- گوشت اضافی برای ماشین کاری
اعمال ضریب انقباض فلز
معمولا اکثر فلزات به هنگام انجماد انقباض حجمی از خود نشان می دهند و قطعه پس از انجماد به طور پیوسته تا رسیدن به دمای محیط منقبض می شود. این انقباض ممکن است تا ۶ درصد نیز برسد. بنابراین در ساختن مدل حتما باید انقباض حجمی فلز منظور شود. نسبت کاستی به حجم قطعه موجود به بیش از ۲ درصد یا ۲۵/۰ اینچ در فوت می رسد. ضریب انقباض برای چند فلز معمول مهندسی به شرح زیر است:
چدن ۸/۰ % الی ۱ %
فولاد ۵/۱ % الی ۲ %
آلومینیم ۱ % الی ۳/۱ %
منیزیم ۱ % الی ۳/۱ %
برنج وبرنز ۵/۱ %
معمولا این ضرایب بر روی خط کش های مخصوص اعمال می شوند که مدل ساز برای ساخت مدل از خط کش مخصوص استفاده می کند.اگر قرار باشد مدل فلزی از روی مدل چوبی ریخته گری شود ، در مدل چوبی علاوه بر ضرایب انقباض قطعه، ضرایب انقباض مدل فلزی نیز منظور می شود.البته استفاده از خط کش های انقباض باید با دقت کافی انجام گیرد، زیرا انقباض حرارتی تنها عامل موثر بر تغییر ابعاد هنگام انجماد نیست. تبدیل های فازی (شامل واکنش های یوتکتویدی، مارتنزیتی و گرافیتی شدن) نیز می توانند موجب انقباض ها یا انبساط های قابل توجهی شوند.
شیب مدل
در ریخته گری مدل های دائمی حتما باید مدل بتواند به راحتی از داخل قالب بیرون بیاید. بنابراین قالب معمولا دو تکه است. رعایت دقت محل جدایش یا سطح جفت شونده دو قسمت قالب بسیار مهم است. همچنین برای سطوحی از مدل که به موازات جهت خروج از قالب هستند، باید شیب مناسبی منظور نمود. اگر سطوح مدل دقیقا به موازات جهت خروج از قالب باشد بر اثر اصطکاک سطوح مدل با دیواره های قالب در موقع درآوردن مدل از قالب سطوح و دیواره های قالب کنده می شود. این اشکال در گوشه ها و زاویه های تیز دیده خواهد شد. برای جلوگیری از این کار در این گونه صفحات شیبی منظور می شود که با شکل ، اندازه و عمق مدل در ماسه متناسب می باشد.
گوشت اضافی برای ماشین کاری
در اکثر قطعات ریختگی ، قطعات بعد از فرآیند ریخته گری، برای رسیدن به صافی سطح مطلوب و اندازه واقعی به انواع مختلفی از عملیات ماشین کاری نیاز خواهند داشت. برای انجام این ماشین کاری ها ابعاد مدل یا قطعه ریخته گری را تا اندازه ای بزرگتر از قطعه واقعی درنظرگرفته می شود.این ابعاد اضافی راگوشت اضافی برای ماشین کاری می نامند.
آماده سازی ماسه قالب گیری
ماسه ای که برای ساخت قالب های ریخته گری به کار می رود عمدتا اکسید سیلیسم(SiO2) است. برای فلزاتی که نقطه ذوب بالایی دارند، از قبیل فولادها، از اکسید زیرکونیم(ZrO2) استفاده می شود.قالبی که از ماسه ساخته می شود باید استحکام کافی برای ریخته گری سالم قطعه مورد نظر را داشته باشد. علاوه بر آن هر ماسه ریخته گری حتما باید دارای مشخصات زیر باشد:
۱- دیر گدازی یا قابلیت تحمل دمای فلز ریخته گری
۲- چسبندگی یا قابلیت نگهداشتن شکل مطلوب پس از قالب گیری
۳- نفوذ پذیری یا قابلیت عبور دادن گازها از خود
۴- قابلیت متلاشی شدن پس از انجماد فلز
برای تعیین مشخصات ماسه آزمایشهای استانداردی روی ماسه انجام می گیرد که عموما پارامترهای زیر را تعیین می کند:
۱- شکل ماده
۲- اندازه دانه
۳- توزیع دانه بندی
۴- دمای ذوب ماسه
۵- ناخالصی های ماسه ( میزان خاک رس و سایر اکسیدهای زود گداز)
۶- سختی، استحکام، نفوذ پذیری بعد از فشرده شدن ( تر و خشک)
۷- تاثیر مقادیر افزودنی ها روی خواص ماسه
مختصری درباره ی فرآیند انجماد در ریخته گری
انجماد عامل ایجاد بسیاری از ویژگی های ساختمانی است که کنترل کننده خواص محصول نهایی هستند. بسیاری از نواقص ریخته گری از قبیل انقباض و تخلخل گازی از فرایند انجماد حاصل می شوند، که با دقت در فرایند و اشراف به نواقص حاصله تا حدود زیادی می توان از شدت این نواقص بکاهیم. هر فرایند انجماد شامل دو مرحله می باشد که عبارتند از : جوانه زنی و رشد.
جوانه زنی
هنگامی که یک ذره جامدوپایداردرمایع مذاب تشکیل شود به این عمل جوانه زنی (هسته سازی) می گوییم.هنگام تبدیل به فاز جامد انرژی داخلی ماده کاهش می یابد ، زیرا در دماهای پایین تر، فاز جامد پایدارتر از فاز مایع است. در همین هنگام سطوح مشترکی بین نطفه های جامد و مایع مذاب اطراف تشکیل می شود که این عمل نیازمند انرژی است. به همین علت جوانه زنی در دمایی که قدری کمتر از نقطه ذوب تعادلی فلز است، شروع می شود. به اختلاف بین دمای نقطه ذوب و دمای شروع جوانه زنی، فوق تبرید می گویند.
دربیشترکارگاه های بزرگ ریخته گری قبل ازریختن مذاب به درون قالب مقداری ناخالصی به آن اضافه می کنند ( به این عمل تلقیح یا پالایش دانه نیز می گویند). دلیل این کار این است که در این حالت انجماد بدون ایجاد یک فصل مشترک کامل گرد هسته صورت می گیرد.معمولا جداره های داخلی قالب و ذرات جامدی که به عنوان ناخالصی وارد مذاب شده اند، این سطوح را تشکیل می دهند. از آنجا که هر جوانه به بلور یا دانه ای در قطعه ریختگی منجر می شود و از طرفی ساختار ریز دانه دارای خواص مکانیکی و استحکام بهتری است، لذا هر عاملی که موجب هسته گذاری شود موجب بالا رفتن کیفیت محصول نهایی می شود. در نتیجه ذرات جامد ناخالصی مکانهای زیاد مناسبی برای جوانه زنی در سرتاسر قطعه به وجود می آورند و در نتیجه محصول ریزدانه و یکنواخت به دست می آید.
رشد
رشد وقتی صورت می گیرد که گرمای نهان ذوب به طور پیوسته از فاز مایع خارج شود.جهت، آهنگ و نوع رشد با با نحوه خارج کردن حرارت از فاز مایع ارتباط دارد. برای جبران نقیصه انقباض ، ماده مذابی که در طرف مایع وجود دارد، به طور پیوسته به طرف قالب جریان می یابد. هرچه آهنگ سرد کردن سریع تر باشد، ماده حاصله ریزدانه تر و در نتیجه دارای خواص مکانیکی بهتری خواهد بود.
|

06-06-2014
|
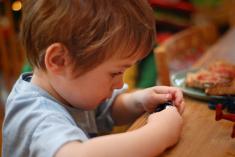 |
مدیر بخش مکانیک - ویندوز و رفع اشکال  
|
|
تاریخ عضویت: Sep 2009
نوشته ها: 2,586
سپاسها: : 5,427
6,159 سپاس در 1,794 نوشته ایشان در یکماه اخیر
|
|
روش ریخته گری دقیق
مزایا و محدودیتها :
الف: مهمترین مزایای روش ریخته گری دقیق عبارتند از : – تولید انبوه قطعات با اشکال پیچیده که توسط روشهای دیگر ریخته گری نمی توان تولید نمود توسط این فرایند امکان پذیر می شود. – مواد قالب و نیز تکنیک بالای این فرایند،- امکان تکرار تولید قطعات با دقت ابعادی وصافی سطح یکنواخت را میدهد. – این روش برای تولید کلیه فلزات و آلیاژهای ریختگی به کار می رود . همچنین امکان تولید قطعاتی از چند آلیاژ مختلف وجود دارد. – توسط این فرآیند امکان تولید قطعاتی با حداقل نیاز به عملایت ماشینکاری و تمام کاری وجود دارد. بنابراین محدودیت استفاده از آلیاژهای با قابلیت ماشینکاری بد از بین می رود. – در این روش امکان تولید قطعات با خصوصا متالورژیکی بهتر وجود دارد. – قالبت تطابق برای ذوب و ریخته گری قطعات در خلاء وجود دارد. – خط جدایش قطعات حذف می شود و نتیجتا موجب حذف عیوبی می شود که در اثر وجود خط جدایش به وجود می آید.. –
ب:مهمترین محدودیتهای روش ریخته گری دقیق عبارتنداز : – اندازه و وزن قطعات تولید شده توسط این روش محدود بوده و عموما قطعات با وزن کمتر از ۵ کیلوگرم تولید می شود . – هزینه تجهیزات و ابزارها در این روش نسبت به سایر روشها بیشتر است.
انواع روشهای ریخته گری دقیق :
در این فرایند دو روش متمایز در تهیه قالب وجود دارد که عبارتند از روش پوسته ای و روش توپر به طور کلی این دو روش درتهیه مدل با هم اختلاف ندارند بلکه در نوع قالبها با هم تفاوت دارند. فرایند قالبهای پوستهای سرامیکی پوسته ای سرامیکی درریخته گری دقیق: برای تولید قعطات ریختگی فولادی ساده کربنی ، فولادهای آلیاژی ،فولاد های زنگ نزن، مقاومت به حرارت ودیگر آلیاژهایی با نقطعه ذوب بالای این روش به کار می رود به طور شماتیک روش تهیه قالب را در این فرآیند نشان می دهند که به ترتیب عبارتند از :
الف : تهیه مدلها : مدلهای مومی یا پلاستیکی توسط ورشهای مخصوص تهیه میشوند.
ب : مونتاژ مدلها : پس از تهیه مدلهای مومی یا پلاستیک معمولا تعدادی از آنها ( این تعداد بستگی به شکل و اندازه دارد) حول یک راهگاه به صورت خوشه ای مونتاژ می شوند در ارتباط باچسباندن مدلها به راهگاه بار ریز روشهای مختلف وجود دارند که سه روش معمولتر است و عبارتند از :
روش اول: محل اتصال در موم مذاب فرو برده می شود و سپس به محل تعیین شده چسبانده می شود .
روش دوم: این روش که به جوشکاری مومی معروف است بدین ترتیب است که محلهای اتصال ذوب شده به هم متصل می گردند .
روش سوم: روش سوم استفاده از چسبهای مخصوص است که محل اتصال توسط جسبهای مخصوص موم یا پلاستیکی به هم چسبانده می شود. روش اتصال مدلهای پلاستیکی نیز شبیه به مدلهای مومی می باشد..
ج : مدل خوشه ای و ضمائم آن در داخل دو غاب سرامیکی فرو برده می شود. درنتیجه یک لایه دو غاب سرامیکی روی مدل را می پوشاند
د:در این مرحله مدل خوشه ای در معرض جریان باران ذرات ماسه نسوز قرار میگیرد.تایک لایه نازک درسطح آن تشکیل شود .
ه: پوسته سرامیکی ایجاده شده در مرحله قبل کاملاخشک می شوند تا سخت و محلم شوند. مراحل ( ج ) (د) ( ه) مجددا برای جند بار تکرار می شود . تعداد دفعات این تکرار بستگی به ضخامت پوسته قالب مورد نیاز دارد. معمولا مراحل اولیه از دوغابهایی که از پودرهای نرم تهیه شده ،استفاده شده و بتدریج می توان از دو غاب و نیز ذرات ماسه نسوز درشت تر استفاده نمود. صافی سطح قطعه ریختگی بستگی به ذرات دو غاب اولیه و نیز ماسه نسوز اولیه دارد.
ز: مدول مومی یا پلاستیکی توسط ذوب یا سوزانده از محفظه قالب خارج می شوند، به این عملیات موم زدایی می گویند . درعملیات موزدایی بایستی توجه نمود که انبساط موم سبب تنش وترک در قالب نشود
ح: در قالبهای تولید شده عملیات بار ریزی مذاب انجام می شود ط: پس از انجماد مذاب ،پوسته سرامیکی شکسته میشود.
ی: در آخرین مرحله قطعات از راهگاه جدا می شوند.
مواد نسوز در فرآیند پوسته ای دقیق:
نوعی سیلیس به دلیل انبساطی حرارتی کم به طور گسترده به عنوان نسوز در روش پوسته ای دقیق مورد استفاده قرار می گیرد.این ماده نسوز برای ریخته گری آلیاژهای آهنی و آلیاژهای کبالت مورد استفاده قرار می گیرد. زیر کنیم شاید بیشترین کاربرد را به عنوان نسوز در فرآیند پوسته ای دارد. این ماده بهترین کیفیت را در سطوح قطعه ایجاد نموده و در درجه حرارتهای بالا پایدار بوده و نسبت به خوردیگ توسط مذاب مقاوم است. آلومین به دلیل مقاومت کم در برابر شوک حرارتی کمتر مورد استفاده قرار میگیرد. به هر حال در برخی موارد به دلیل مقاومت در درجه حرارت بالا ( تا حدودc ْ۱۷۶۰ مورد استفاده قرار می گیرد.
چسبها :مواد نسوز به وسیله چسبها به یکدیگر می چسبد این چسبها معمولا شیمیایی می باشند سلیکات اتیل ،سیلیکات سدیم و سیلیس کلوئیدی . سیلیکات اتیل باعث پیدایش سطح تمام شده بسیار خوب میشوند. سیلیس کلوئیدی نیز باعث بوجود آمدن سطح تمام شده عالی می شود.
اجزای دیگر: یک ترکیب مناسب علاوه بر مواد فوق شامل مواد دیگری است که هر کدام به منظور خاصی استفاده می شود.
این مواد به این شرح است : – مواد کنترل کننده ویسکوزیته – مواد ترکننده جهت کنترل سیالیت دو غاب و قابلیت مرطوب سازی مدل – مواد ضد کف جهت خارج کردن حبابهای هوا – مواد ژلاتینی جهت کنترل در خشک شدن و تقلیل ترکها فرایند تهیه قالبهای توپر در ریخته گری دقیق: شکل به طول شماتیک مراحل تهیه قالب به روش توپر را نشان می دهد که عبارتند از :
الف : تهیه مدلهای ذوب شونده
ب :مونتاژ مدلها : این عملیات درقسمت
ج: توضیح داده شده ح: مدلهای خوشه ای و ضمائم آن درداخل درجه ای قرار میگیرد و دوغاب سرامیکی اطراف آن ریخته میشودتا درجه با دو غاب دیرگداز پر شود. به این دو غاب دو غاب پشت بند نیز گفته میشود . این دو غاب در هوا سخت می شود و بدین ترتیب قالب به اصطلاح توپر تهیه می شود
د: عملیات بار ریزی انجام میشود
ه : قالب سرامیکی پس ازانجماد مذاب شکسته می شود
و: قطعات از راهگاه جدا می شوند شکل دادن به روش ریخته گری دو غابی مقدمه این طریقه شبیه کار ***** پرس است ، به این معنا که مقدار آب به مواد اولیه اضافه شده تا حالت دو غابی به خود بگیرد. باید خارج شود ،به این دلیل برای ساختن اشیا روش کندی است . به طور کلی این روش موقعی مورد استفاده قرار میگیرد که شکل دادن به روشهای اقتصادی تر غیر ممکن باشد. ازطرف دیگر مواقعی از این روش اسفتاده می کنند که تعدااد زیادی از قطعه مورد درخاواست نباشد . برتری بارز این روش در تولید قطعات پیچیده است . دوغاب،داخل قالبهای گچی متخلخل که شکل مورد نظر را دارد، ریخته می شود . آب دو غاب جذب قالب شده و دراثر این عمل یک لایه از مواد دو غاب به دیواره قالب بسته می شود و شکل داخل قالب را به خود می گیرد.دو غاب در داخلی قالب باقی می ماند تا زمانی که لایه ضخامت مورد نظر را پیدا کند. اگر ریخته گری تو خالی نباشد ،نیازی به تخلیه دو غاب نیست ، ولی برای قطعاتی که توخالی باشند، قالب برگدانده میشود . دو غاب اضافی که روی سطح قالب قرار دارد،به وسیله کرادکی تراشیده می شود . سپس لایه اضافی با کمک چاقو در ناحیه ذخیره برداشته می شود . جدارة تشکیل دشه که همان قطعه نهایی موردنظر است، درقالب باقی می ماند تا زمانی که کمی منقبض شده و از قالب جدا شود. سپس می توان آن را از قالب در آورد . بعد از اینکه قطعه مورد نظر خشک شد،کلیه خطوط اضافی که دراثر قالب روی آن ایجاد شده است، با چاقو زده و یا به وسیله اسفنج تمیز می شود در این مرحله قطعه آماده پخت است . چون آب اضافی دو غاب حین ریخته گری خارج شده ، سطح دو غاب در داخل قالب پایین می آید. به این دلیل معمولا یک حلقه بالای قالب تعبیه می شود تا دو غاب را بالای قعطه مورد نظر نگه دارد. این حلقه ممکن است از گچ و یا از لاستیک ساخته شود . اگر ازگچ ساخه شود ، داخل آن نیز دو غاب به جدا بسه شده و با کمک چاقو تراشیده میشود. وقتی که جسم داخل قالب گچی کمی خشک شد،اسفنجی نمدار دور آن کشیده می شود تا سطحی صاف به دست آید . این روش که در بالا به ان اشاره شد ، برای ریخته گری اجسامی است که داخل آنها خالی است . مانند گلدان، زیر سیگاری ، و غیره … اما طریقه ای هم هست که برای ساختن اجسام توپر به کار می رود ، به این تریتب که دو غاب داخل قالب می ماند تا اینکه تمام آن سف شود. برای ساختن اشیایی که شکل پیچیده دارند ، ممکن است قالب گچی ازچندین قعطه ساخته شود تا بتوانیم جسم داخل آن را از قالب خارج کنیم ، هر قطعه قالب شامل جای خالی است که قعطه قالب دیگر در آن جا می گیرد. (نروماده ) اگر قالب دارای قطعات زیادباشد،لازم است در حین ریخته گری خوب به هم چسبد این کار را می توان به وسیله نوار لاستیک که محکم به دور آن می بندیم انجام دهیم . هنگام در اوردن جسم از قالب باید این نوار لاستیکی را باز کرده و برداریم. غلظت مواد ریخته گری باید به اندازه کافی باشد که باعث اشباع شدن قالب از آب نشود . بخصوص موادی که شامل مقدار زیادی خاک رس هستند،غلظت آنها به قدری کم خواهد شد که ریخته گری آنها مشکل شده و معایبی هم در حین ریخته گری ایجادمی شود. برای اینکه دو غاب را به اندازه کافی روان کنیم . مواد روانسازی به دو غاب اضافه می شود.
ریخته گری دو غابی تجهیزات مورد نیاز: مواد مورد نیاز – مواد اولیه – آب – روانساز( سودا و سیلیکات سدیم یا آب شیشه ) ابزار مورد نیاز – همزان الکتریکی – ترازو ( با دقت ۱/۰و۰۱/۰ گرم) – پارچ دردار – قالب گچی مورد نیاز ( قالب قوری – لوله و قالب هاون آزمایشگاهی – دسته هاون آزمایشگاهی – دسته هاون ) – ویسکوزیته متر ریزشی با بروکفید – لاستیک نواری – میز کار آماده سازی دو غاب توزین و اختلاط مواد اولیه :در تولید فرآورده های سرامیکی ،عمل توزین مواد اولیه به طور کلی می تواند به دو روش انجام شود. (توزین به روش خشک ) (توزین به روش تر )در مرحله تهیه و آماده سازی بدنه ،روش توزین عامل بسیار مهم و تعیین کننده ای است.
ویرایش توسط bigbang : 06-06-2014 در ساعت 04:06 PM
|

06-06-2014
|
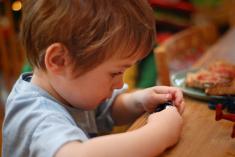 |
مدیر بخش مکانیک - ویندوز و رفع اشکال  
|
|
تاریخ عضویت: Sep 2009
نوشته ها: 2,586
سپاسها: : 5,427
6,159 سپاس در 1,794 نوشته ایشان در یکماه اخیر
|
|
روش ریخته گری دقیق
توزین درحالت خشک : در این روش ،عمل توزین هنگامی صورت می گیرد که مواد اولیه به صورت خشک و یا تقریبا خشک باشند و هنوز تبدیل به دو غاب نشده باشند . هنگام توزین ،حتما باید آب موجود درمواد اولیه و به طور عمده در مواد پلاستیک (که از محیط اطراف جذب شده و یا در معدن در اثر ریزش برف و باران مرطوب و نمدار شده است )منظور شود . البته باید توجه داشت که تعیین دقیق مقدار رطوبت موجود در مواد اولیه،عملا غیر ممکن است و این موضوع ، یعنی عدم دقت ، نقص بزرگ توزین به روش خشک است . در عمل از تک تک مواد اولیه نمونه برداری کنید ،و بعد از توزین آن را در خشک کن آزمایشگاهی در دمای ( ) قرار دهید بعد از ۲۴ ساعت نمونه را دوباهر توزین کنید . اختلاف وزن نسبت به وزن اولیه را محاسبه کنید تا درصد رطوبت خاک مشخص شود . بعد از تعیین درصد رطوبت ، درصد فوق را در توزین نهایی مواد اولیه منظور کنید . توزین در حالت تر: در این روش،عمل توزین بعد از تبدیل هر یک از مواد اولیه به دو غاب انجام می شود. بدیهی است که هریک از مواد اولیه به دو غاب انجام می شود . بدیهی است که در روش خشک گفته شد ، وجود نخواهد داشت . البته در صنعت به لحاظ نیاز این روش به چاله های ذخیره سازی که فضای بیشتری با سرماهی گذاری اولیه بالاتری را می طلبد ،کمتر استقبال می شود. در مورد توزین به روش تر ،حتما این روش مطرح خواهد شد که چگونه می توان به مقدار مواد خشک موجود در دو غاب هر یک از مواد اولیه پی برد. در عمل برای تعیین مقدار مواد خشک موجود درغابها از رابطه برونینارت استفاده می شود . W=(p-1) W= وزن ماده خشک موجود در یک سانتیمتر مکعب از دو غاب (گرم ) P= وزن ماده خشک موجود در یک سانتیمتر مکعب = وزن مخصوص ( دانسیته ) دو غاب درعمل با توزین حجم مشخصی از دو غابها،می توان به وزن مخصوص یا دانسیته آنها پی برد. در مورد وزن مخصوص مواد خشک باید اشاره شود که به طور معمول این مقدار حدود ۵/۲ تا۶/۲ گرم بر سانتیمتر مکعب است. بنابرانی اگر با تقریب ،وزن مخصوص را ۵/۲ اختیار کنید ، مقدار کسری برابر با خواهد بود . پس تنها عامل در اکثر موارد،دانسیته دو غابها است .
الک کردن : عمل توزین مواد اولیه چه به صورت تر باشد و چه در حالت خشک ،ابعاد ذرات دو غاب بدنه موجود در حوضچه های اختلاط نباید از حدو مورد نظر بزرگتر باشد. تعیین ابعاد ذرات موجود در دو غاب،قسسمتی از اعمال روزمره آزمایشگاهها ی خطوط تولید است و این عمل در پایان نمونه برداری در حین سایش انجام گیرد و سپس تخلیه انجام می گیرد. در هر صورت ،انتخاب دانه بندی مناسب بستگی به فاکتور های ذیل دارد: – نوع بدنه ( چینی ظروف- چینی بهداشتی ،- نوز) – نوع مواد اولیه و درصد انها (- بالکی) – خواص ریخته گری ( تیکسوتراپی ،- سرعت ریخته گری) – جذب آب – عمل الک کردن برای جداسازی ذرات درشت و کنترل خواص دوغاب بسیار ضروری است. زیرا اولا وجود ذرات درشت عوارض گسترده ای بر پروسس ریخته گری ،- خواص دو غاب ،- خواص حین پخت و خواص محصول نهایی دارد. ثانیا ،- کنترل دانه بندی برای خواص دو غاب شدیدا تحت تاثیر دانه بندی بوده و نباید از حد متعارفی کمتر باشد . انتخاب و شماره الک توسط استاد کار انجام خواهد شد. عموما به لحاظ وجود ذرات درشت و حضور ناخالصیهای گسترده در مواد اولیه نظیر موادآلی ،ریشه درختان ،کرک و پشم که به منظور افزایش استحکام خام به بعضی از مواد اولیه زده می شود ،غالبا چشمه های الک زود کورمی شود و ادامه عمل الک کردن را با مشکل مواجه می کند. لذا غالبا الکهارا چند طبقه منظور کرده و طبقات نیز از مش کوچک به مش بزرگ از بالا به پایین قرار می گیرند تا دانه های درشت تر بالاو دانه های کمتری روی الک زیرین که دارای چشمه های ریزتری است ،قرار گیرد .
آهن گیری: می دانید که اهن با ظرفیتهای مختلف در مواد اولیه یا بدنه های خام وجود دارد، در مجموع چهار شکل متفاوت آهن وجود دارد. – به صورت یک کاتیون در داخل شبکه بلوری مواد اولیه – به صورت کانیهای مختلف که به عنوان ناخالصیهای طبیعی با مواد اولیه مخلوط می شوند . – به صورت ناخالصیهای مصنوعی که در اثر سایش صفحات خرد کننده سنگ شکنها و آسیابها به وجود آمده اند . فقط در حالت اخیر آهن به صورت فلزی یا آزاد وجود دارد. لذا در این حالت توانایی می توان عمل اهن گیری را انجام داد. – به صورت ترکیبات دو وسه ظرفیتی آهن که در اثر زنگ زدگی خطوط انتقال دو غاب ،- وارد دوغاب میشوند.در تولید فرآورده های ظریف برای تخلیص دو غاب از ذرات آهن موجود ،- از دستگاههای آهنر یا مگنت دستی استفاده می شود . دستگاههای آهنربا اگر چه عامل بسیار موثری در حذف آهن و تخلیص دو غاب هستند،- ولی ماسفانه باید توجه داشت که این دستگاهها قادر به جذب تمام مواد وذرات حاوی آهن نیستند . در بین کانیهای مهم آهن، کانیهای مگنیت سیدریت و هماتیت به ترتیب دارای بیشترین خاصیت مغناطیسی هستند و بنابراین ،به وسیله دستگاههای آهنربا جذب می شوند . در کانیهای لیمونیت مارکاسیت و پیریت خاصیت مغناطیسی به ترتیب کاهش یافته و به همین دلیل در عمل ، احتمال جدا سازی این کانیها به وسیله دستگاههای آهنربا بسیار کم است . در مورد آهن فلزی بدیهی است که دستگاههای آهنربا به راحتی قادر به جذب آنها هستند. تنظیم خواص رئولوژیکی بعد از اینکه دو غاب الک و آهنگیری شد، دو غاب رابه چاله ذخیره یا به ظرف مخصوص انتقال می دهیم . در حالی که همزن الکتریکی با دور کم در حال هم زدن آرام دو غاب است ، از چاله نمونه برداری کرده و آزمونهای زیر را اعمال می کنیم تا فرم پیوست تکمیل شود. همان طوریکه در فرم ملاحظه می شود ،
شامل مراحل زیر است :اولین مرحله تنظیم دانسیته دوغاب است . بدین معنا که سرعت ریخته گری یا مدت زمانی که لازم است دو غاب در قالب گچی بماند و به ضخامت مورد نظر برسد، تنظیم شود . بدین منظور در ابتدا قالب گچی مناسب را که دارای عمر مشخص و درصد آب به گچ ثابت و معینی است آماده می کنیم و یا اینکه می توانیم از یک مدل مشخص در خط تولید استفاده کنیم بعد از بستن قطعات قالب، آنها را با کمک یک نوار پهن لاستیکی نظیر تیوپ دوچرخه یا لاستیکی که از تیوپ ماشین معمولی بریده شده است ، کاملا در کنار هم جذب و محکم کنید . دو غاب حاصل را به داخل قالب گچی بریزید . و بعد از مدت زمان مشخصی ،در نتیجه واکنشهای متقابل بین دو غالب وقالب گچی ،لایه ای درمحل تماس دو غاب و قالب ایجاد می شود .واضح است که قطر لایه ایجاد شده بستگی به زمان توقف دو غالب در قالب دارد. بعد از گذشت مدت زمان مورد نظر ، دو غاب اضافی موجود قالب تخلیه می شود . این زمان به طور عمده بستگی به قطر فراورده مورد نظر وسرعت ریخته گری دو غاب دارد . باید توجه داشت که تراکم قالب گچی نیز عامل موثری در زمان ریخته گری است . ولی برای ایجاد زمینه ای در ذهن دانش آموزان باید اشاره شود که با توجه به کلیه عوامل موثر زمان ریخته گری به عنوان مثال برای فرآورده ها بهداشتی به قطر حدود ۱۰ یا ۱۱میلیمتر،معمولا حدود تا ۲ ساعت ،برای ظروف غذا خوری از جنس ارتن و ریا پرسلان با قطر۲ تا ۳ میلیمتر ، حدود ۱۵ تا ۲۵ دقیقه و برای چینی استخوانی به همین قطر حدود ۲ تا ۵ دقیقه است .سپس قالب و فرآورده شکل یافته در آن برای مدتی به حال خود گذاشته می شود تا لایه ایجاد شده ،تا حدودی خشک و در نتیجه کوچکتر شود .(دراثر انقباض تر به خشک ) بعد از این مرحله قطعه شکل یافته به راحتی از قالب جدا شده و می توان آ نرا از داخل قالب گچی خارج کرد درهنگام تشکیل لایه در محل تماس قالب و دوغاب،حجم دو غاب موجود در غاب به مرور کمتر وکمتر می شود . به همین دلیل لازم است که مجددا مقادیری دو غاب به داخل قالب گچی ریخته شود. با توجه به اینکه انجام این عمل نیازمند نیروی انسانی بیشتر و نیز مراقیت دایم است، در عمل قطعه ای در دهانه قالب گچی تعبیه شده که اصطلاحا به آن ((حلقه ۴۵)) گفته می شود. این حلقه باعث ایجاد ستونی از دو غاب برفراز قطعه ساخته شده می شود. در نتیجه با کاهش حجم دو غاب موجود در قالب ،نیازی به اضافه کردن مجدد دو غاب نیست. در بعضی موارد به جای تعبیه حلقه از قیف استفاده می شود . حلقه ها می توانند از جنس لاستیک و یا گچ باشند. در صورتی که حلقه ها از جنس گچ باشند، در سطح داخلی حلقه ،در محل تماس دو غاب با گچ نیز لایه ای ایجاد میشود . این لایه اضافی و نیز دیگر قسمتهای اضافی ( به عنوان مثال اضافات ایجاد شده در محل درز قالبها)در مرحله پرداخت بریده و جدا می شوند . قالبهای گچی به ندرت یک تکه هستند. بدین معنی که معمولا فراورده ها در قالبهای چند تکه شکل می یابند. از طرف دیگر در مورد بعضی از شکلهای پیچیده لازم است مدل اصلی به چند قعطه مختلف تجزیه شده و هر یک از قسمتها جداگانه شکل بگیرند . سپس، بعد از خروج از قالبها به یکدیگر متصل شوند. به عنوان مثال ، در مورد ظروف خانگی دسته فنجانها و یا لوله قوریها به صورت مجزا شکل یافته و پس از خروج از قالب، به بدنه اصلی چسبانده می شوند . مرحله چسباندن قطعات در شکل دادن فراورده ها دارای اهمیت زیاد است . درشکل دادن به روش ریخته گری به صورت کاملا ساده نشان داده شده است . تعیین زمان ریخته گری دو غابی وسایل مورد نیاز مواد اولیه مورد نیاز تعداد پنج عدد قالب گچی دو غاب تنظیم شده لیوانی کولیس یا ریز سنج کاغذ میلیمتری سیم یا فنر برای برش دادن خط کش کرنومتر مدت زمانی که دو غاب در داخل قالب باقی می ماند ، در قطر لایه ایجاد شده ویا به عبارت دیگر در ضخامت بدنه خام ، تاثیر بسیار زیادی دارد. بدنی معنی که چنانچه دو غاب اضافی همچنان در قالب باقی مانده و تخلیه نشود و اصطلاحا (( زمان بیشتر به دو غاب داده شود ))،قطر لایه ایجاد شده افزایش خواهدیافت . باید توجه داشت که با گذشت زمان ،سرعت تشکیل ثابت نبوده و به مرورکند تر می شود . چرا که در این شرایط ،خود لایه ایجاد شده به صورت سدی در ماقابل نفوذ آب به داخل گچ ،عمل می کند. همچنانکه مشاهده می شود ، این عامل که اصطلاح (( ریخته گری)) به آن اتلاق می شود، عامل مهمی درتعیین قطر بدنه خام (ودر نتیجه دیگر خصوصیات بدنه ) و نیز سرعت تولید است . به همین دلیل ،یکی از مهمترین خواص دوغابها مقدار ( سرعت ریخته گری) آنها است. به طور مشخص ،سرعت ریخته گری عبارت است از ضخامت ایجاد شده در واحد زمان و عوامل موثر در ان کلا عبارتند از : فشار، درجه حرارت ،وزن مخصوص دو غاب و بالاخره مقاومت لایه ریخته گری شده در برابر عبورآب . دو عامل اخیر وبخصوص آخرین عامل ، مهمترین مواردی هستندکه عملادرصنعت مورد توجه قرار می گیرند . مقاومت لایه ریخته گری شده در برابر عبور آب ، خود به عوامل دیگری بستگی دارد که به طور خلاصه عبارتند از:نوع و یا دانه بندی مواد و نیز چگونگی و یا شدت روان شدگی ( به عبارت دیگر تجمع و یاتفرق ذرات )ضمنا باید توجه داشت که در سرعت ریخته گری ،عوامل خارجی دیگری که ربطی به خواص دو غاب ندارند نیز موثر هستند. مانند تراکم و یا تخلخل قالب گچی و درصد رطوبت موجود در آن.ضخامت لایه ایجاد شده رابطه مستقیم با جذر زمان ریخته گری دارد. بنابراین ،بین زمان و ضخامت لایه رابطه زیر بر قرار خواهد بود: ویا در رابطه فوق ، ۱ضخامت لایه ایجاد شده ( به میلی متر )و t زمان (به دقیقه)وk ضریب ثابت است . به همین دلیل سرعت ریخته گری معمولا به صورت بیان می شود . رابطه فوق بدین معنی است که به عنوان مثال چنانچه ساخت فرآورده ای به ضخامت یک میلیمتر ،چهاردقیقه زمان احتیاج داشته باشد، ساخت فراورده دیگر به ضخامت ۲ میلیمتر در همان شرایط به شانزده دقیقه زمان نیاز دارد. با این توضیحات ، برای تعیین سرعت ریخته گری و در کنار آن زمان ریخته گری، به صورت زیر عمل کنید: نخست روی قالبهای گچی به ترتیب شماره یک تا پنج بزنید ، سپس دو غاب را به ترتیب در اولین قالب ریخته و بلافاصله کرنومتر را بزنید .بلافاصله قالب گچی دیگر و درنهایت پنجمین قالب گچی را از دو غاب پرکنید. بعد از یک دقیقه اولین قالب را و بعد بترتیب زیرا قالبهای دیگر را تخلیه کنید : بعد از اینکه آخرین قطرات دو غاب از چکه کردن باز ایستاد ،قالب را به حال خود بگذارید و بعد از زمان مشخصی که جداره تشکیل شده در اثر انقباض از قالب جدا شد، آن را از قالب بیرون آورد. با ریز سنج یا با کمک کولیس اندازه گیری کنید.سپس با کمک کاغذ میلیمتر و با انتخاب دو محور xوy به ترتیبx را به عنوان زمان و y را به عنوان ضخامت با کمک نقطعه یابی رسم کنید. در این حالت با رسم ۱ بر حسب خواهید توانست ضریب خط را بدست آورید که همان سرعت ریخته گری است . و از انجا می تونید به راحتی هر ضخامتی را که می خواهید ، تعیین و زمان آن را محاسبه کنید. مثلا اگر سرعت ریخته گری ۵/۰ باشد،یعنی ( میلیمتر مربع بر دقیقه) برای داشتن بدنه ای به ضخامت ۸/۰ سانتیمتر به صورت زیر محاسبه می کنیم . دقیقه َ ۲٫۸ = ۶۰ ÷ ۱۲۸ یعنی باید ۲ ساعت و ۸ دقیقه زمان بدهید تا جداره مورد نظر تشکیل شود.یکی از عوامل موثر درسرعت ریخته گری ، وزن مخصوص دو غاب و یا به عبارت دیگر نسبت بین مواد جامد و آب است . علاوه بر این مورد افزایش مقار اب در دو غاب ریخته گری باعث اشباع سریعتر قالبها می شود که به نوبه خود خشک کردن کامل قالبها باعث فرسودگی سریعتر آنها و نهایتا کاهش بازدهی قالبهامی شود . وزن مخصوص دو غابهای ریخته گری باید حتی المقدور بالا باشد. علت اساسی استفاده از روان کننده ها در دوغابهای ریخته گری ،همین مورد است . چرا که بدون استفاده از روان کننده ها تهیه دو غابهایی با وزن مخصوص بالا ، تقریباً غیر ممکن است . به همین دلیل یکی از خواص مخصوص آنها است . در تولید فرآورده های سرامیک ظریف به طور معمول وزن مخصوص دو غاب ریخته گری بین ۵/۱ تا است. یکی دیگر از خصوصیات بسیار مهم در دو غابهای ریتخه گری و یسکوزیته آنهاست .ویکسوزیته یک دو غاب علی رغم وزن مخصوص بسیار بالای آن باید درحدی باشد که درمقیاس صنعتی ، دوغاب به راحتی از الکها و یا خطوط لوله عبور کند و درعین حال بتواند تمامی زوایاو گوشه های قالب را پرکند. مساله مهم درارتباط بین وزن مخصوص ویسکوزیته و روان کننده این موضوع است که اگر چه تغییرات وزن مخصوص ویا به عبارت دیگر مقدار آب و نیز تغییرات مقدار روان کننده در ویسکوزیته موثر هستند. ولی تغییرات مقدار روان کننده در مقدار وزن مخصوص بیتایر است ودر نتیجه در خطوط تولید کارخانه ها ،با اندازه گیری و یسکوزیته و وزن مخصوص در بسیاری موارد می توان به تغییرات مقدار روان کننده پی برد. علاوه برسرعت ریخته گری ،وزن مخصوص و ویسکوزیته عامل دیگری نیز دردو غاب بدنه خام اهمیت دارد و آن تیکسو تروپی است ؛ خاصیت تیکسوتر را به طور خلاصه می توان به صورت «افزایش ویسکوزیته دو غاب دراثر سکون و رکود و کاهش ویسکوزیته دراثر هم خوردن» تعریف کرد. دو غابی که دارای تیکسوتر و پی زیادی است بلافاصله بعد از هم خوردن ممکن است دارای روانی مناسبی باشد. ولی بعد از مدتی سکون ، ویسکوزیته آن به شدت افزایش می یابد. افزایش ویسکوزیته در اثر خاصیت تیکسوتروپی، گاه به حدی است که چنانچه ظرف حاوی دو غاب بعد از مدتی سکون ،وارونه شود، دو غاب داخل آن از ظرف خارج نمی شود. در دو غابهای ریخته گری به طور معمول مقادیر کمی تیکسوتروپی مطلوب است. چراکه تیکسوتروپی باعث افزایش سرعت ریخته گری شده و درعین حال استحکام و ثبات خاصی را در قطعه ریخته گری شده ایجاد می کند.( باید دقت شود که منظور ، ایجاد استحکام و در حالت پلاستیک است ( درصورتی که استحکام خشک مد نظر باشد، خلاف این موضوع صحیح است . بدین معنی است که رسهای روان شده به دلیل تراکم بیشتر دارای استحکام خشک بسیار بیشتری هستند. استحکام خشک زیادتر فرآروده هایی که به روش ریخته گری شکل می یابند نیز به همین دلیل است ). از طرف دیگر وجود مقدار زیادی تیکسوتروپی دردوغاب نیز باعث بروز اشکالاتی می شود؛ تیکسوتروپی زیاد در دو غاب باعث سست شدن فراورده ریختهگری می شود ،به نحوی که چنین فرآورده هایی را می توان به راحتی تغییر شکل داده و با تکان دادن ممکن است مجددا به دو غاب تبدیل شوند. به عنوان یک قانون کلی ، روان کننده ها نه تنها باعث کاهش ویکسوزیته می شوند، بلکه تیکسوتروپی رانیز کاهش می دهند. بنابراین ،مقدار مصرف روان کننده باید به نحوی تنظیم شود که با ایجاد بیشترین مقدار روانی ، مقادیر کمی تیکسوتروپی در دو غاب ایجاد شود. دلیل استفاده مشترک از سلیکات و کربنات سدیم به عنوان روان کننده همین مورد است. سیلیکات سدیم اگر چه باعث روانی دو غاب می شود. ولی تیکسوتروپی ار ینز به طور کامل از بین می برد . در حالی که کربنات سدیم درعین حال که باعث کاهش ویسکوزیته می شود، مقادیر کمی تیکسوتروپی در دو غاب باقی میگذارد. استفاده توام از این دو روان کننده باعث ایجاد بیشترین حد روانی و در عین حال وجود مقدار کمی تیکسوتروپی در دو غاب می شود.
روشهای ساخت ماهیچه های سرامیکی: ماهیچه های سرامیکی به خاطر دقت ابعادی بالا در ریخته گری قطعات دقیق به کاربرده می شوند. این ماهیچه ها به دو روش دو غابی و فشاری ساخته می شوند که از نظر نوع نسوز یکسان بوده ولی چسبهای آنها با هم تفاوت دارد. دو روش ساخت ماهیچه ها در ذیل به اختصار شرح داده می شود:
الف ) ماهیچه های ساخت سرامیک به روش دو غابی در این روش یک مدول مومی به شکل ماهیچه موردنظر ( با احتساب انقباضات موم و مواد سرامیکی پس از خشک شدن) ساخه می شوند. پس این مدل مومی را در داخل یک قالب می گذاریم به طوریکه یک قسمت از مدل جهت خروج موم و وارد کردن دو غاب سرامیک به آن درنظر گرفته شود. پس دو غاب گچی آماده شده را در درون قالب حاوی مدل مومی می ریزیم و پس ازسفت شدن دو غاب گچ آنرا از قالب خارج کرده و در خشک کن قرار می دهیم پس از خشک شدن قالب گچی مدل مومی را ذوب کرده و از قالب گچی خارج می نماییم. دو غاب سرامیکی تهیه شده به نسبت ۷۰% پودر نسوز و ۳۰% آب را درون قالب گچی تهیه شده می ریزیم و پس ازخشک شدن مواد سرامیکی قالب گچی را شکسته و ماهیچه سرامیکی شکل گرفته را خارج می نماییم . این ماهیچه را پس از خشک کردن در دمایی حدود۹۵۰ درجه سانتی گراد پخت می کنیم. ماهیچه تهیه شده پس از پخت کامل و خنک شدن آماده استفاده می باشد. قابل ذکر است که چسبهای مورد استفاده دراین روش از نوع سیلیکاتها می باشد ونسوز مصرفی دارای عدد ریز دانگی ۲۰۰یا۳۲۵ مش است.
بـ )ساخت ماهیچه های سرامیکی به روش فشاری: در این روش پودر نسوز مورداستفاده که ازنوع زیرکنی یا آلومینیایی یا آلومیناسیلیکاتی می باشد را با رزین مخصوص(موم و..)مخلوط کرده و به صورت خمیر در می آوریم خمیر تهیه شده ار در درون قالب ماهیچه که عمدتااز جنس فلز می باشدبه روش فشاری تزریق می کنیم . ماهیچه تهیه شده را حرارت داده تا به آرامی موم آن خارج گردد. سپس این ماهیچه رادر دمای ۹۵۰ درجه سانتیگراد تحت عملیات نهایی پخت قرار می دهیم. پس ازپخت کامل ماهیچه و خنک نمودن آن تا دمای محیط ماهیچه مذکور مورد استفاده قرار می گیرد.
ویرایش توسط bigbang : 06-06-2014 در ساعت 04:15 PM
|

06-06-2014
|
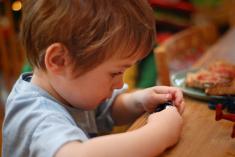 |
مدیر بخش مکانیک - ویندوز و رفع اشکال  
|
|
تاریخ عضویت: Sep 2009
نوشته ها: 2,586
سپاسها: : 5,427
6,159 سپاس در 1,794 نوشته ایشان در یکماه اخیر
|
|
ریخته گری در قالب دوغابی
ریخته گری در قالب دوغابی
مزایا و محدودیتها
الف: مهمترین مزایای روش ریخته گری دقیق عبارتند از : – تولید انبوه قطعات با اشکال پیچیده که توسط روشهای دیگر ریخته گری نمی توان تولید نمود توسط این فرایند امکان پذیر می شود. – مواد قالب و نیز تکنیک بالای این فرایند،- امکان تکرار تولید قطعات با دقت ابعادی وصافی سطح یکنواخت را میدهد. – این روش برای تولید کلیه فلزات و آلیاژهای ریختگی به کار می رود . همچنین امکان تولید قطعاتی از چند آلیاژ مختلف وجود دارد. – توسط این فرآیند امکان تولید قطعاتی با حداقل نیاز به عملایت ماشینکاری و تمام کاری وجود دارد. بنابراین محدودیت استفاده از آلیاژهای با قابلیت ماشینکاری بد از بین می رود. – در این روش امکان تولید قطعات با خصوصا متالورژیکی بهتر وجود دارد. – قالبت تطابق برای ذوب و ریخته گری قطعات در خلاء وجود دارد. – خط جدایش قطعات حذف می شود و نتیجتا موجب حذف عیوبی می شود که در اثر وجود خط جدایش به وجود می آید.. –
ب:مهمترین محدودیتهای روش ریخته گری دقیق عبارتنداز : – اندازه و وزن قطعات تولید شده توسط این روش محدود بوده و عموما قطعات با وزن کمتر از ۵ کیلوگرم تولید می شود . – هزینه تجهیزات و ابزارها در این روش نسبت به سایر روشها بیشتر است.
انواع روشهای ریخته گری دقیق: در این فرایند دو روش متمایز در تهیه قالب وجود دارد که عبارتند از روش پوسته ای و روش توپر به طور کلی این دو روش درتهیه مدل با هم اختلاف ندارند بلکه در نوع قالبها با هم تفاوت دارند. فرایند قالبهای پوستهای سرامیکی پوسته ای سرامیکی درریخته گری دقیق: برای تولید قعطات ریختگی فولادی ساده کربنی ، فولادهای آلیاژی ،فولاد های زنگ نزن، مقاومت به حرارت ودیگر آلیاژهایی با نقطعه ذوب بالای این روش به کار می رود به طور شماتیک روش تهیه قالب را در این فرآیند نشان می دهند که به ترتیب عبارتند از :
الف : تهیه مدلها : مدلهای مومی یا پلاستیکی توسط ورشهای مخصوص تهیه میشوند.
ب : مونتاژ مدلها : پس از تهیه مدلهای مومی یا پلاستیک معمولا تعدادی از آنها ( این تعداد بستگی به شکل و اندازه دارد) حول یک راهگاه به صورت خوشه ای مونتاژ می شوند در ارتباط باچسباندن مدلها به راهگاه بار ریز روشهای مختلف وجود دارند که سه روش معمولتر است و عبارتند از :
روش اول: محل اتصال در موم مذاب فرو برده می شود و سپس به محل تعیین شده چسبانده می شود .
روش دوم: این روش که به جوشکاری مومی معروف است بدین ترتیب است که محلهای اتصال ذوب شده به هم متصل می گردند .
روش سوم: روش سوم استفاده از چسبهای مخصوص است که محل اتصال توسط جسبهای مخصوص موم یا پلاستیکی به هم چسبانده می شود. روش اتصال مدلهای پلاستیکی نیز شبیه به مدلهای مومی می باشد..
ج : مدل خوشه ای و ضمائم آن در داخل دو غاب سرامیکی فرو برده می شود. درنتیجه یک لایه دو غاب سرامیکی روی مدل را می پوشاند
د:در این مرحله مدل خوشه ای در معرض جریان باران ذرات ماسه نسوز قرار میگیرد.تایک لایه نازک درسطح آن تشکیل شود .
ه: پوسته سرامیکی ایجاده شده در مرحله قبل کاملاخشک می شوند تا سخت و محلم شوند. مراحل ( ج ) (د) ( ه) مجددا برای جند بار تکرار می شود . تعداد دفعات این تکرار بستگی به ضخامت پوسته قالب مورد نیاز دارد. معمولا مراحل اولیه از دوغابهایی که از پودرهای نرم تهیه شده ،استفاده شده و بتدریج می توان از دو غاب و نیز ذرات ماسه نسوز درشت تر استفاده نمود. صافی سطح قطعه ریختگی بستگی به ذرات دو غاب اولیه و نیز ماسه نسوز اولیه دارد.
ز: مدول مومی یا پلاستیکی توسط ذوب یا سوزانده از محفظه قالب خارج می شوند، به این عملیات موم زدایی می گویند . درعملیات موزدایی بایستی توجه نمود که انبساط موم سبب تنش وترک در قالب نشود
ح: در قالبهای تولید شده عملیات بار ریزی مذاب انجام می شود ط: پس از انجماد مذاب ،پوسته سرامیکی شکسته میشود.
ی: در آخرین مرحله قطعات از راهگاه جدا می شوند.
مواد نسوز در فرآیند پوسته ای دقیق:
نوعی سیلیس به دلیل انبساطی حرارتی کم به طور گسترده به عنوان نسوز در روش پوسته ای دقیق مورد استفاده قرار می گیرد.این ماده نسوز برای ریخته گری آلیاژهای آهنی و آلیاژهای کبالت مورد استفاده قرار می گیرد. زیر کنیم شاید بیشترین کاربرد را به عنوان نسوز در فرآیند پوسته ای دارد. این ماده بهترین کیفیت را در سطوح قطعه ایجاد نموده و در درجه حرارتهای بالا پایدار بوده و نسبت به خوردیگ توسط مذاب مقاوم است. آلومین به دلیل مقاومت کم در برابر شوک حرارتی کمتر مورد استفاده قرار میگیرد. به هر حال در برخی موارد به دلیل مقاومت در درجه حرارت بالا ( تا حدودc ْ۱۷۶۰ مورد استفاده قرار می گیرد.
چسبها :مواد نسوز به وسیله چسبها به یکدیگر می چسبد این چسبها معمولا شیمیایی می باشند سلیکات اتیل ،سیلیکات سدیم و سیلیس کلوئیدی . سیلیکات اتیل باعث پیدایش سطح تمام شده بسیار خوب میشوند. سیلیس کلوئیدی نیز باعث بوجود آمدن سطح تمام شده عالی می شود.
اجزای دیگر: یک ترکیب مناسب علاوه بر مواد فوق شامل مواد دیگری است که هر کدام به منظور خاصی استفاده می شود.
این مواد به این شرح است : – مواد کنترل کننده ویسکوزیته – مواد ترکننده جهت کنترل سیالیت دو غاب و قابلیت مرطوب سازی مدل – مواد ضد کف جهت خارج کردن حبابهای هوا – مواد ژلاتینی جهت کنترل در خشک شدن و تقلیل ترکها فرایند تهیه قالبهای توپر در ریخته گری دقیق: شکل به طول شماتیک مراحل تهیه قالب به روش توپر را نشان می دهد که عبارتند از :
الف : تهیه مدلهای ذوب شونده
ب :مونتاژ مدلها : این عملیات درقسمت
ج: توضیح داده شده ح: مدلهای خوشه ای و ضمائم آن درداخل درجه ای قرار میگیرد و دوغاب سرامیکی اطراف آن ریخته میشودتا درجه با دو غاب دیرگداز پر شود. به این دو غاب دو غاب پشت بند نیز گفته میشود . این دو غاب در هوا سخت می شود و بدین ترتیب قالب به اصطلاح توپر تهیه می شود
د: عملیات بار ریزی انجام میشود
ه : قالب سرامیکی پس ازانجماد مذاب شکسته می شود
و: قطعات از راهگاه جدا می شوند شکل دادن به روش ریخته گری دو غابی مقدمه این طریقه شبیه کار ***** پرس است ، به این معنا که مقدار آب به مواد اولیه اضافه شده تا حالت دو غابی به خود بگیرد. باید خارج شود ،به این دلیل برای ساختن اشیا روش کندی است . به طور کلی این روش موقعی مورد استفاده قرار میگیرد که شکل دادن به روشهای اقتصادی تر غیر ممکن باشد. ازطرف دیگر مواقعی از این روش اسفتاده می کنند که تعدااد زیادی از قطعه مورد درخاواست نباشد . برتری بارز این روش در تولید قطعات پیچیده است . دوغاب،داخل قالبهای گچی متخلخل که شکل مورد نظر را دارد، ریخته می شود . آب دو غاب جذب قالب شده و دراثر این عمل یک لایه از مواد دو غاب به دیواره قالب بسته می شود و شکل داخل قالب را به خود می گیرد.دو غاب در داخلی قالب باقی می ماند تا زمانی که لایه ضخامت مورد نظر را پیدا کند. اگر ریخته گری تو خالی نباشد ،نیازی به تخلیه دو غاب نیست ، ولی برای قطعاتی که توخالی باشند، قالب برگدانده میشود . دو غاب اضافی که روی سطح قالب قرار دارد،به وسیله کرادکی تراشیده می شود . سپس لایه اضافی با کمک چاقو در ناحیه ذخیره برداشته می شود . جدارة تشکیل دشه که همان قطعه نهایی موردنظر است، درقالب باقی می ماند تا زمانی که کمی منقبض شده و از قالب جدا شود. سپس می توان آن را از قالب در آورد . بعد از اینکه قطعه مورد نظر خشک شد،کلیه خطوط اضافی که دراثر قالب روی آن ایجاد شده است، با چاقو زده و یا به وسیله اسفنج تمیز می شود در این مرحله قطعه آماده پخت است . چون آب اضافی دو غاب حین ریخته گری خارج شده ، سطح دو غاب در داخل قالب پایین می آید. به این دلیل معمولا یک حلقه بالای قالب تعبیه می شود تا دو غاب را بالای قعطه مورد نظر نگه دارد. این حلقه ممکن است از گچ و یا از لاستیک ساخته شود . اگر ازگچ ساخه شود ، داخل آن نیز دو غاب به جدا بسه شده و با کمک چاقو تراشیده میشود. وقتی که جسم داخل قالب گچی کمی خشک شد،اسفنجی نمدار دور آن کشیده می شود تا سطحی صاف به دست آید . این روش که در بالا به ان اشاره شد ، برای ریخته گری اجسامی است که داخل آنها خالی است . مانند گلدان، زیر سیگاری ، و غیره … اما طریقه ای هم هست که برای ساختن اجسام توپر به کار می رود ، به این تریتب که دو غاب داخل قالب می ماند تا اینکه تمام آن سف شود. برای ساختن اشیایی که شکل پیچیده دارند ، ممکن است قالب گچی ازچندین قعطه ساخته شود تا بتوانیم جسم داخل آن را از قالب خارج کنیم ، هر قطعه قالب شامل جای خالی است که قعطه قالب دیگر در آن جا می گیرد. (نروماده ) اگر قالب دارای قطعات زیادباشد،لازم است در حین ریخته گری خوب به هم چسبد این کار را می توان به وسیله نوار لاستیک که محکم به دور آن می بندیم انجام دهیم . هنگام در اوردن جسم از قالب باید این نوار لاستیکی را باز کرده و برداریم. غلظت مواد ریخته گری باید به اندازه کافی باشد که باعث اشباع شدن قالب از آب نشود . بخصوص موادی که شامل مقدار زیادی خاک رس هستند،غلظت آنها به قدری کم خواهد شد که ریخته گری آنها مشکل شده و معایبی هم در حین ریخته گری ایجادمی شود. برای اینکه دو غاب را به اندازه کافی روان کنیم . مواد روانسازی به دو غاب اضافه می شود.
ریخته گری دو غابی تجهیزات مورد نیاز: مواد مورد نیاز – مواد اولیه – آب – روانساز( سودا و سیلیکات سدیم یا آب شیشه ) ابزار مورد نیاز – همزان الکتریکی – ترازو ( با دقت ۱/۰و۰۱/۰ گرم) – پارچ دردار – قالب گچی مورد نیاز ( قالب قوری – لوله و قالب هاون آزمایشگاهی – دسته هاون آزمایشگاهی – دسته هاون ) – ویسکوزیته متر ریزشی با بروکفید – لاستیک نواری – میز کار آماده سازی دو غاب توزین و اختلاط مواد اولیه :در تولید فرآورده های سرامیکی ،عمل توزین مواد اولیه به طور کلی می تواند به دو روش انجام شود. (توزین به روش خشک ) (توزین به روش تر )در مرحله تهیه و آماده سازی بدنه ،روش توزین عامل بسیار مهم و تعیین کننده ای است.
توزین درحالت خشک : در این روش ،عمل توزین هنگامی صورت می گیرد که مواد اولیه به صورت خشک و یا تقریبا خشک باشند و هنوز تبدیل به دو غاب نشده باشند . هنگام توزین ،حتما باید آب موجود درمواد اولیه و به طور عمده در مواد پلاستیک (که از محیط اطراف جذب شده و یا در معدن در اثر ریزش برف و باران مرطوب و نمدار شده است )منظور شود . البته باید توجه داشت که تعیین دقیق مقدار رطوبت موجود در مواد اولیه،عملا غیر ممکن است و این موضوع ، یعنی عدم دقت ، نقص بزرگ توزین به روش خشک است . در عمل از تک تک مواد اولیه نمونه برداری کنید ،و بعد از توزین آن را در خشک کن آزمایشگاهی در دمای ( ) قرار دهید بعد از ۲۴ ساعت نمونه را دوباهر توزین کنید . اختلاف وزن نسبت به وزن اولیه را محاسبه کنید تا درصد رطوبت خاک مشخص شود . بعد از تعیین درصد رطوبت ، درصد فوق را در توزین نهایی مواد اولیه منظور کنید . توزین در حالت تر: در این روش،عمل توزین بعد از تبدیل هر یک از مواد اولیه به دو غاب انجام می شود. بدیهی است که هریک از مواد اولیه به دو غاب انجام می شود . بدیهی است که در روش خشک گفته شد ، وجود نخواهد داشت . البته در صنعت به لحاظ نیاز این روش به چاله های ذخیره سازی که فضای بیشتری با سرماهی گذاری اولیه بالاتری را می طلبد ،کمتر استقبال می شود. در مورد توزین به روش تر ،حتما این روش مطرح خواهد شد که چگونه می توان به مقدار مواد خشک موجود در دو غاب هر یک از مواد اولیه پی برد. در عمل برای تعیین مقدار مواد خشک موجود درغابها از رابطه برونینارت استفاده می شود . W=(p-1) W= وزن ماده خشک موجود در یک سانتیمتر مکعب از دو غاب (گرم ) P= وزن ماده خشک موجود در یک سانتیمتر مکعب = وزن مخصوص ( دانسیته ) دو غاب درعمل با توزین حجم مشخصی از دو غابها،می توان به وزن مخصوص یا دانسیته آنها پی برد. در مورد وزن مخصوص مواد خشک باید اشاره شود که به طور معمول این مقدار حدود ۵/۲ تا۶/۲ گرم بر سانتیمتر مکعب است. بنابرانی اگر با تقریب ،وزن مخصوص را ۵/۲ اختیار کنید ، مقدار کسری برابر با خواهد بود . پس تنها عامل در اکثر موارد،دانسیته دو غابها است .
الک کردن : عمل توزین مواد اولیه چه به صورت تر باشد و چه در حالت خشک ،ابعاد ذرات دو غاب بدنه موجود در حوضچه های اختلاط نباید از حدو مورد نظر بزرگتر باشد. تعیین ابعاد ذرات موجود در دو غاب،قسسمتی از اعمال روزمره آزمایشگاهها ی خطوط تولید است و این عمل در پایان نمونه برداری در حین سایش انجام گیرد و سپس تخلیه انجام می گیرد. در هر صورت ،انتخاب دانه بندی مناسب بستگی به فاکتور های ذیل دارد: – نوع بدنه ( چینی ظروف- چینی بهداشتی ،- نوز) – نوع مواد اولیه و درصد انها (- بالکی) – خواص ریخته گری ( تیکسوتراپی ،- سرعت ریخته گری) – جذب آب – عمل الک کردن برای جداسازی ذرات درشت و کنترل خواص دوغاب بسیار ضروری است. زیرا اولا وجود ذرات درشت عوارض گسترده ای بر پروسس ریخته گری ،- خواص دو غاب ،- خواص حین پخت و خواص محصول نهایی دارد. ثانیا ،- کنترل دانه بندی برای خواص دو غاب شدیدا تحت تاثیر دانه بندی بوده و نباید از حد متعارفی کمتر باشد . انتخاب و شماره الک توسط استاد کار انجام خواهد شد. عموما به لحاظ وجود ذرات درشت و حضور ناخالصیهای گسترده در مواد اولیه نظیر موادآلی ،ریشه درختان ،کرک و پشم که به منظور افزایش استحکام خام به بعضی از مواد اولیه زده می شود ،غالبا چشمه های الک زود کورمی شود و ادامه عمل الک کردن را با مشکل مواجه می کند. لذا غالبا الکهارا چند طبقه منظور کرده و طبقات نیز از مش کوچک به مش بزرگ از بالا به پایین قرار می گیرند تا دانه های درشت تر بالاو دانه های کمتری روی الک زیرین که دارای چشمه های ریزتری است ،قرار گیرد .
|

06-06-2014
|
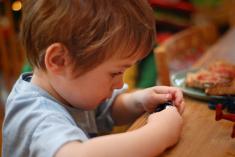 |
مدیر بخش مکانیک - ویندوز و رفع اشکال  
|
|
تاریخ عضویت: Sep 2009
نوشته ها: 2,586
سپاسها: : 5,427
6,159 سپاس در 1,794 نوشته ایشان در یکماه اخیر
|
|
ریخته گری در قالب دوغابی
آهن گیری: می دانید که اهن با ظرفیتهای مختلف در مواد اولیه یا بدنه های خام وجود دارد، در مجموع چهار شکل متفاوت آهن وجود دارد. – به صورت یک کاتیون در داخل شبکه بلوری مواد اولیه – به صورت کانیهای مختلف که به عنوان ناخالصیهای طبیعی با مواد اولیه مخلوط می شوند . – به صورت ناخالصیهای مصنوعی که در اثر سایش صفحات خرد کننده سنگ شکنها و آسیابها به وجود آمده اند . فقط در حالت اخیر آهن به صورت فلزی یا آزاد وجود دارد. لذا در این حالت توانایی می توان عمل اهن گیری را انجام داد. – به صورت ترکیبات دو وسه ظرفیتی آهن که در اثر زنگ زدگی خطوط انتقال دو غاب ،- وارد دوغاب میشوند.در تولید فرآورده های ظریف برای تخلیص دو غاب از ذرات آهن موجود ،- از دستگاههای آهنر یا مگنت دستی استفاده می شود . دستگاههای آهنربا اگر چه عامل بسیار موثری در حذف آهن و تخلیص دو غاب هستند،- ولی ماسفانه باید توجه داشت که این دستگاهها قادر به جذب تمام مواد وذرات حاوی آهن نیستند . در بین کانیهای مهم آهن، کانیهای مگنیت ( ) سیدریت ( )و هماتیت( ) به ترتیب دارای بیشترین خاصیت مغناطیسی هستند و بنابراین ،به وسیله دستگاههای آهنربا جذب می شوند . در کانیهای لیمونیت ( ) مارکاسیت و پیریت ( ) خاصیت مغناطیسی به ترتیب کاهش یافته و به همین دلیل در عمل ، احتمال جدا سازی این کانیها به وسیله دستگاههای آهنربا بسیار کم است . در مورد آهن فلزی بدیهی است که دستگاههای آهنربا به راحتی قادر به جذب آنها هستند. تنظیم خواص رئولوژیکی بعد از اینکه دو غاب الک و آهنگیری شد، دو غاب رابه چاله ذخیره یا به ظرف مخصوص انتقال می دهیم . در حالی که همزن الکتریکی با دور کم در حال هم زدن آرام دو غاب است ، از چاله نمونه برداری کرده و آزمونهای زیر را اعمال می کنیم تا فرم پیوست تکمیل شود. همان طوریکه در فرم ملاحظه می شود ،
شامل مراحل زیر است :اولین مرحله تنظیم دانسیته دوغاب است . بدین معنا که سرعت ریخته گری یا مدت زمانی که لازم است دو غاب در قالب گچی بماند و به ضخامت مورد نظر برسد، تنظیم شود . بدین منظور در ابتدا قالب گچی مناسب را که دارای عمر مشخص و درصد آب به گچ ثابت و معینی است آماده می کنیم و یا اینکه می توانیم از یک مدل مشخص در خط تولید استفاده کنیم بعد از بستن قطعات قالب، آنها را با کمک یک نوار پهن لاستیکی نظیر تیوپ دوچرخه یا لاستیکی که از تیوپ ماشین معمولی بریده شده است ، کاملا در کنار هم جذب و محکم کنید . دو غاب حاصل را به داخل قالب گچی بریزید . و بعد از مدت زمان مشخصی ،در نتیجه واکنشهای متقابل بین دو غالب وقالب گچی ،لایه ای درمحل تماس دو غاب و قالب ایجاد می شود .واضح است که قطر لایه ایجاد شده بستگی به زمان توقف دو غالب در قالب دارد. بعد از گذشت مدت زمان مورد نظر ، دو غاب اضافی موجود قالب تخلیه می شود . این زمان به طور عمده بستگی به قطر فراورده مورد نظر وسرعت ریخته گری دو غاب دارد . باید توجه داشت که تراکم قالب گچی نیز عامل موثری در زمان ریخته گری است . ولی برای ایجاد زمینه ای در ذهن دانش آموزان باید اشاره شود که با توجه به کلیه عوامل موثر زمان ریخته گری به عنوان مثال برای فرآورده ها بهداشتی به قطر حدود ۱۰ یا ۱۱میلیمتر،معمولا حدود تا ۲ ساعت ،برای ظروف غذا خوری از جنس ارتن و ریا پرسلان با قطر۲ تا ۳ میلیمتر ، حدود ۱۵ تا ۲۵ دقیقه و برای چینی استخوانی به همین قطر حدود ۲ تا ۵ دقیقه است .سپس قالب و فرآورده شکل یافته در آن برای مدتی به حال خود گذاشته می شود تا لایه ایجاد شده ،تا حدودی خشک و در نتیجه کوچکتر شود .(دراثر انقباض تر به خشک ) بعد از این مرحله قطعه شکل یافته به راحتی از قالب جدا شده و می توان آ نرا از داخل قالب گچی خارج کرد درهنگام تشکیل لایه در محل تماس قالب و دوغاب،حجم دو غاب موجود در غاب به مرور کمتر وکمتر می شود . به همین دلیل لازم است که مجددا مقادیری دو غاب به داخل قالب گچی ریخته شود. با توجه به اینکه انجام این عمل نیازمند نیروی انسانی بیشتر و نیز مراقیت دایم است، در عمل قطعه ای در دهانه قالب گچی تعبیه شده که اصطلاحا به آن ((حلقه ۴۵)) گفته می شود. این حلقه باعث ایجاد ستونی از دو غاب برفراز قطعه ساخته شده می شود. در نتیجه با کاهش حجم دو غاب موجود در قالب ،نیازی به اضافه کردن مجدد دو غاب نیست. در بعضی موارد به جای تعبیه حلقه از قیف استفاده می شود . حلقه ها می توانند از جنس لاستیک و یا گچ باشند. در صورتی که حلقه ها از جنس گچ باشند، در سطح داخلی حلقه ،در محل تماس دو غاب با گچ نیز لایه ای ایجاد میشود . این لایه اضافی و نیز دیگر قسمتهای اضافی ( به عنوان مثال اضافات ایجاد شده در محل درز قالبها)در مرحله پرداخت بریده و جدا می شوند . قالبهای گچی به ندرت یک تکه هستند. بدین معنی که معمولا فراورده ها در قالبهای چند تکه شکل می یابند. از طرف دیگر در مورد بعضی از شکلهای پیچیده لازم است مدل اصلی به چند قعطه مختلف تجزیه شده و هر یک از قسمتها جداگانه شکل بگیرند . سپس، بعد از خروج از قالبها به یکدیگر متصل شوند. به عنوان مثال ، در مورد ظروف خانگی دسته فنجانها و یا لوله قوریها به صورت مجزا شکل یافته و پس از خروج از قالب، به بدنه اصلی چسبانده می شوند . مرحله چسباندن قطعات در شکل دادن فراورده ها دارای اهمیت زیاد است . درشکل دادن به روش ریخته گری به صورت کاملا ساده نشان داده شده است . تعیین زمان ریخته گری دو غابی وسایل مورد نیاز مواد اولیه مورد نیاز تعداد پنج عدد قالب گچی دو غاب تنظیم شده لیوانی کولیس یا ریز سنج کاغذ میلیمتری سیم یا فنر برای برش دادن خط کش کرنومتر مدت زمانی که دو غاب در داخل قالب باقی می ماند ، در قطر لایه ایجاد شده ویا به عبارت دیگر در ضخامت بدنه خام ، تاثیر بسیار زیادی دارد. بدنی معنی که چنانچه دو غاب اضافی همچنان در قالب باقی مانده و تخلیه نشود و اصطلاحا (( زمان بیشتر به دو غاب داده شود ))،قطر لایه ایجاد شده افزایش خواهدیافت . باید توجه داشت که با گذشت زمان ،سرعت تشکیل ثابت نبوده و به مرورکند تر می شود . چرا که در این شرایط ،خود لایه ایجاد شده به صورت سدی در ماقابل نفوذ آب به داخل گچ ،عمل می کند. همچنانکه مشاهده می شود ، این عامل که اصطلاح (( ریخته گری)) به آن اتلاق می شود، عامل مهمی درتعیین قطر بدنه خام (ودر نتیجه دیگر خصوصیات بدنه ) و نیز سرعت تولید است . به همین دلیل ،یکی از مهمترین خواص دوغابها مقدار ( سرعت ریخته گری) آنها است. به طور مشخص ،سرعت ریخته گری عبارت است از ضخامت ایجاد شده در واحد زمان و عوامل موثر در ان کلا عبارتند از : فشار، درجه حرارت ،وزن مخصوص دو غاب و بالاخره مقاومت لایه ریخته گری شده در برابر عبورآب . دو عامل اخیر وبخصوص آخرین عامل ، مهمترین مواردی هستندکه عملادرصنعت مورد توجه قرار می گیرند . مقاومت لایه ریخته گری شده در برابر عبور آب ، خود به عوامل دیگری بستگی دارد که به طور خلاصه عبارتند از:نوع و یا دانه بندی مواد و نیز چگونگی و یا شدت روان شدگی ( به عبارت دیگر تجمع و یاتفرق ذرات )ضمنا باید توجه داشت که در سرعت ریخته گری ،عوامل خارجی دیگری که ربطی به خواص دو غاب ندارند نیز موثر هستند. مانند تراکم و یا تخلخل قالب گچی و درصد رطوبت موجود در آن.ضخامت لایه ایجاد شده رابطه مستقیم با جذر زمان ریخته گری دارد. بنابراین ،بین زمان و ضخامت لایه رابطه زیر بر قرار خواهد بود: ویا در رابطه فوق ، ۱ضخامت لایه ایجاد شده ( به میلی متر )و t زمان (به دقیقه)وk ضریب ثابت است . به همین دلیل سرعت ریخته گری معمولا به صورت بیان می شود . رابطه فوق بدین معنی است که به عنوان مثال چنانچه ساخت فرآورده ای به ضخامت یک میلیمتر ،چهاردقیقه زمان احتیاج داشته باشد، ساخت فراورده دیگر به ضخامت ۲ میلیمتر در همان شرایط به شانزده دقیقه زمان نیاز دارد. با این توضیحات ، برای تعیین سرعت ریخته گری و در کنار آن زمان ریخته گری، به صورت زیر عمل کنید: نخست روی قالبهای گچی به ترتیب شماره یک تا پنج بزنید ، سپس دو غاب را به ترتیب در اولین قالب ریخته و بلافاصله کرنومتر را بزنید .بلافاصله قالب گچی دیگر و درنهایت پنجمین قالب گچی را از دو غاب پرکنید. بعد از یک دقیقه اولین قالب را و بعد بترتیب زیرا قالبهای دیگر را تخلیه کنید : بعد از اینکه آخرین قطرات دو غاب از چکه کردن باز ایستاد ،قالب را به حال خود بگذارید و بعد از زمان مشخصی که جداره تشکیل شده در اثر انقباض از قالب جدا شد، آن را از قالب بیرون آورد. با ریز سنج یا با کمک کولیس اندازه گیری کنید.سپس با کمک کاغذ میلیمتر و با انتخاب دو محور xوy به ترتیبx را به عنوان زمان و y را به عنوان ضخامت با کمک نقطعه یابی رسم کنید. در این حالت با رسم ۱ بر حسب خواهید توانست ضریب خط را بدست آورید که همان سرعت ریخته گری است . و از انجا می تونید به راحتی هر ضخامتی را که می خواهید ، تعیین و زمان آن را محاسبه کنید. مثلا اگر سرعت ریخته گری ۵/۰ باشد،یعنی ( میلیمتر مربع بر دقیقه) برای داشتن بدنه ای به ضخامت ۸/۰ سانتیمتر به صورت زیر محاسبه می کنیم . دقیقه َ ۲٫۸ = ۶۰ ÷ ۱۲۸ یعنی باید ۲ ساعت و ۸ دقیقه زمان بدهید تا جداره مورد نظر تشکیل شود.یکی از عوامل موثر درسرعت ریخته گری ، وزن مخصوص دو غاب و یا به عبارت دیگر نسبت بین مواد جامد و آب است . علاوه بر این مورد افزایش مقار اب در دو غاب ریخته گری باعث اشباع سریعتر قالبها می شود که به نوبه خود خشک کردن کامل قالبها باعث فرسودگی سریعتر آنها و نهایتا کاهش بازدهی قالبهامی شود . وزن مخصوص دو غابهای ریخته گری باید حتی المقدور بالا باشد. علت اساسی استفاده از روان کننده ها در دوغابهای ریخته گری ،همین مورد است . چرا که بدون استفاده از روان کننده ها تهیه دو غابهایی با وزن مخصوص بالا ، تقریباً غیر ممکن است . به همین دلیل یکی از خواص مخصوص آنها است . در تولید فرآورده های سرامیک ظریف به طور معمول وزن مخصوص دو غاب ریخته گری بین ۵/۱ تا است. یکی دیگر از خصوصیات بسیار مهم در دو غابهای ریتخه گری و یسکوزیته آنهاست .ویکسوزیته یک دو غاب علی رغم وزن مخصوص بسیار بالای آن باید درحدی باشد که درمقیاس صنعتی ، دوغاب به راحتی از الکها و یا خطوط لوله عبور کند و درعین حال بتواند تمامی زوایاو گوشه های قالب را پرکند. مساله مهم درارتباط بین وزن مخصوص ویسکوزیته و روان کننده این موضوع است که اگر چه تغییرات وزن مخصوص ویا به عبارت دیگر مقدار آب و نیز تغییرات مقدار روان کننده در ویسکوزیته موثر هستند. ولی تغییرات مقدار روان کننده در مقدار وزن مخصوص بیتایر است ودر نتیجه در خطوط تولید کارخانه ها ،با اندازه گیری و یسکوزیته و وزن مخصوص در بسیاری موارد می توان به تغییرات مقدار روان کننده پی برد. علاوه برسرعت ریخته گری ،وزن مخصوص و ویسکوزیته عامل دیگری نیز دردو غاب بدنه خام اهمیت دارد و آن تیکسو تروپی است ؛ خاصیت تیکسوتر را به طور خلاصه می توان به صورت «افزایش ویسکوزیته دو غاب دراثر سکون و رکود و کاهش ویسکوزیته دراثر هم خوردن» تعریف کرد. دو غابی که دارای تیکسوتر و پی زیادی است بلافاصله بعد از هم خوردن ممکن است دارای روانی مناسبی باشد. ولی بعد از مدتی سکون ، ویسکوزیته آن به شدت افزایش می یابد. افزایش ویسکوزیته در اثر خاصیت تیکسوتروپی، گاه به حدی است که چنانچه ظرف حاوی دو غاب بعد از مدتی سکون ،وارونه شود، دو غاب داخل آن از ظرف خارج نمی شود. در دو غابهای ریخته گری به طور معمول مقادیر کمی تیکسوتروپی مطلوب است. چراکه تیکسوتروپی باعث افزایش سرعت ریخته گری شده و درعین حال استحکام و ثبات خاصی را در قطعه ریخته گری شده ایجاد می کند.( باید دقت شود که منظور ، ایجاد استحکام و در حالت پلاستیک است ( درصورتی که استحکام خشک مد نظر باشد، خلاف این موضوع صحیح است . بدین معنی است که رسهای روان شده به دلیل تراکم بیشتر دارای استحکام خشک بسیار بیشتری هستند. استحکام خشک زیادتر فرآروده هایی که به روش ریخته گری شکل می یابند نیز به همین دلیل است ). از طرف دیگر وجود مقدار زیادی تیکسوتروپی دردوغاب نیز باعث بروز اشکالاتی می شود؛ تیکسوتروپی زیاد در دو غاب باعث سست شدن فراورده ریختهگری می شود ،به نحوی که چنین فرآورده هایی را می توان به راحتی تغییر شکل داده و با تکان دادن ممکن است مجددا به دو غاب تبدیل شوند. به عنوان یک قانون کلی ، روان کننده ها نه تنها باعث کاهش ویکسوزیته می شوند، بلکه تیکسوتروپی رانیز کاهش می دهند. بنابراین ،مقدار مصرف روان کننده باید به نحوی تنظیم شود که با ایجاد بیشترین مقدار روانی ، مقادیر کمی تیکسوتروپی در دو غاب ایجاد شود. دلیل استفاده مشترک از سلیکات و کربنات سدیم به عنوان روان کننده همین مورد است. سیلیکات سدیم اگر چه باعث روانی دو غاب می شود. ولی تیکسوتروپی ار ینز به طور کامل از بین می برد . در حالی که کربنات سدیم درعین حال که باعث کاهش ویسکوزیته می شود، مقادیر کمی تیکسوتروپی در دو غاب باقی میگذارد. استفاده توام از این دو روان کننده باعث ایجاد بیشترین حد روانی و در عین حال وجود مقدار کمی تیکسوتروپی در دو غاب می شود.
روشهای ساخت ماهیچه های سرامیکی: ماهیچه های سرامیکی به خاطر دقت ابعادی بالا در ریخته گری قطعات دقیق به کاربرده می شوند. این ماهیچه ها به دو روش دو غابی و فشاری ساخته می شوند که از نظر نوع نسوز یکسان بوده ولی چسبهای آنها با هم تفاوت دارد. دو روش ساخت ماهیچه ها در ذیل به اختصار شرح داده می شود:
الف ) ماهیچه های ساخت سرامیک به روش دو غابی در این روش یک مدول مومی به شکل ماهیچه موردنظر ( با احتساب انقباضات موم و مواد سرامیکی پس از خشک شدن) ساخه می شوند. پس این مدل مومی را در داخل یک قالب می گذاریم به طوریکه یک قسمت از مدل جهت خروج موم و وارد کردن دو غاب سرامیک به آن درنظر گرفته شود. پس دو غاب گچی آماده شده را در درون قالب حاوی مدل مومی می ریزیم و پس ازسفت شدن دو غاب گچ آنرا از قالب خارج کرده و در خشک کن قرار می دهیم پس از خشک شدن قالب گچی مدل مومی را ذوب کرده و از قالب گچی خارج می نماییم. دو غاب سرامیکی تهیه شده به نسبت ۷۰% پودر نسوز و ۳۰% آب را درون قالب گچی تهیه شده می ریزیم و پس ازخشک شدن مواد سرامیکی قالب گچی را شکسته و ماهیچه سرامیکی شکل گرفته را خارج می نماییم . این ماهیچه را پس از خشک کردن در دمایی حدود۹۵۰ درجه سانتی گراد پخت می کنیم. ماهیچه تهیه شده پس از پخت کامل و خنک شدن آماده استفاده می باشد. قابل ذکر است که چسبهای مورد استفاده دراین روش از نوع سیلیکاتها می باشد ونسوز مصرفی دارای عدد ریز دانگی ۲۰۰یا۳۲۵ مش است.
بـ )ساخت ماهیچه های سرامیکی به روش فشاری: در این روش پودر نسوز مورداستفاده که ازنوع زیرکنی یا آلومینیایی یا آلومیناسیلیکاتی می باشد را با رزین مخصوص(موم و..)مخلوط کرده و به صورت خمیر در می آوریم خمیر تهیه شده ار در درون قالب ماهیچه که عمدتااز جنس فلز می باشدبه روش فشاری تزریق می کنیم . ماهیچه تهیه شده را حرارت داده تا به آرامی موم آن خارج گردد. سپس این ماهیچه رادر دمای ۹۵۰ درجه سانتیگراد تحت عملیات نهایی پخت قرار می دهیم. پس ازپخت کامل ماهیچه و خنک نمودن آن تا دمای محیط ماهیچه مذکور مورد استفاده قرار می گیرد.
ویرایش توسط bigbang : 06-06-2014 در ساعت 04:12 PM
|

06-06-2014
|
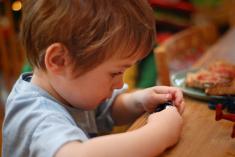 |
مدیر بخش مکانیک - ویندوز و رفع اشکال  
|
|
تاریخ عضویت: Sep 2009
نوشته ها: 2,586
سپاسها: : 5,427
6,159 سپاس در 1,794 نوشته ایشان در یکماه اخیر
|
|
ریخته گری فولاد و تاریخچه آن
ریخته گری فولاد و تاریخچه آن
در فولاد ریزی دو روش عمده ریخته گری داریم :
۱- روش شمش ریزی: که ریخته گری جهت تولید آلیاژ انجام می شود.
۲- شکل ریزی: که ریخته گری جهت تولید قطعه انجام می شود.
تاریخچه فولاد سازی
فولاد نوعی آهن است که بیشتر ناخالصی های آن جدا شده است . آهن عنصری ،فلزی مستحکم، سخت ،سنگین و به رنگ خاکستری است. این ماده در شهاب سنگ ها یافت می گردد. همچنین آهن در ترکیب با بسیاری از کانی ها در پوسته زمین پیدا می شود. آهن به آسانی زنگ می زند و می توان آن را مغناطیسی ساخت وبه شدت جذب آهنربا نمود. از این ماده جهت ساختن بسیاری از سازه ها استفاده می گردد. فولاد (آهن ذوب شده) با گرمای شدید و آمیختن آن با کربن (آلیاژ) درست می شود . از فولاد برای ساختن ماشین آلات ، اتو مبیل ، ابزار آلات و دیگر مصنوعات استفاده می گردد.
تاریخ ذوب آهن و آهن کاری به درازای خود تاریخ است . باستان شناسان در مصر ابزارهایی آهنی یافتند که تاریخ ساخت آنها به ۳۰۰۰ سال پیش از میلاد مسیح بر می گردد، و زیور آلات آهنی حتی پیش از این تاریخ نیز به کار می رفت . اسلحه های آهنین ساخته شده به وسیله تیمار گرمایی برای یونانیان در ۱۰۰۰ سال پیش از میلاد امری شناخته شده بود.
آهن ورزیده (چکش خوار)
وسایل آهنی اولیه و آنهایی که تا سده ی چهاردهم ساخته می شد تحت عنوان آهن ورزیده رده بندی می گردد. آنها را با گرما دادن توده های سنگ معدن آهن و زغال چوب در کوره ی آهنگری یا کوره های آهن دارای تهویه مصنوعی تولید می کردند. تحت این تیمار ، سنگ معدن احیا و اسفنجی از آهن فلز و لجنی (سر باره ای ) حاوی نا خالصی های فلزی و خاکستر چوب تبدیل می شد . این اسفنج آهنی را از کوره بیرون می آورند در حالی که هنوز گداخته و ملتهب بود و آن را با پتک های سنگین می کوبیدند تا سرباره و جوش از آن خارج شود و به آهن جامد تبدیل شود.
آهنی که تحت این شرایط تولید می شد حاوی ۳ درصد ذرات سرباره و ۱/۰ درصد دیگر ناخالصی ها بود . گاه این تکنیک آهن سازی بر حسب تصادف به جای آهن چکش خوار فولاد واقعی به دست می داد. آهنگران آموخته اند که با گرما دادن آهن چکش خوار و ذغال چوب در بوته های سفالین به مدت چندین روز فولاد به دست آورنده طی این فرایند آهن کربن کافی جذب می کرد تا به فولاد واقعی تبدیل گردد.
آهن لخته (خام یا شمش)
پس از سده چهار دهم اندازه کوره هایی که برای ذوب آهن به کار می رفت افزایش یافت ، و از کشش اضافی برای بافشار وارد کردن گازهای حاصل از احتراق به درون((بار)) کوره حاوی آمیزه ی مواد خام استفاده می شد .در این کوره های وسیع تر ،سنگ آهن در بخش بالایی کوره نخست به آهن فلزی تبدیل می شد و سپس به علت گازهایی که با فشار وارد آن می شد با کربن بیشتری آمیخته می گردید. ابزارهای اولیه آهنی که تا سده ی چهاردهم ساخته می شد تحت نام آهن چکش خوار دسته بندی می گردد. فراورده های این کوره ها آهن لخته بود ، آلیاژی که در دمای پایین تری نسبت به آهن چکش خوار ذوب می شود. آهن لخته (چدن خام) (بدان علت به این اسم نامگذاری شده که معمولا آن را در شمش های کوتاه وپهن که تحت عنوان قالب فلزی یا بلوک نامیده می شود می ساختند) وسپس تصفیه ی بیشتری روی آن انجام می شد تا به فولاد تبدیل شود.
دم و کوره های الکتریکی
امروزه برای ذوب آهن از کوره های دم دار استفاده می شود که در واقع نوع بهبود یافته کوره هایی است که آهنگران قدیم برای تهیه ی آهن به کار می بردند. فرایند تصفیه آهن گداخته به کمک جریان هوا به وسیله مخترعی انگلیسی به نام سر هنری بسمر تکمیل گردید که کوره بسمر یا کونورتور (کوره مخصوص تولید فولاد) را در سال ۱۸۵۵ اختراع کرد.
چگونه فولاد می سازیم
کارخانه های فولاد از چهار واحد اولیه ی یکپارچه درست شده است شامل:
· احیای مستقیم
· کوره ی قوس الکترونیکی
· ریخته گری پیوسته (متوالی)
· کارخانه نورد
هر یک از واحد ها واحد بعدی را تغذیه می کند.
کارخانه احیای مستقیم با استفاده از ساچمه های سنگ معدن آهن جامد تولید می کنند.
اولی گاز طبیعی را به هیدروژن و مونوکسید کربن تبدیل می کند . این گازها اکسیژن را از سنگ معدن گرم شده در کوره می زدایند و سنگ آهن را به آهن فلزی تبدیل می کنند.گاز/آب خنک کننده در بخش پایین کوره جریان می یابد و آهن را سرد می کند.
طی این فرایند چیزی تولید می شود که آهن مستقیما احیا شده نام دارد (DRI) واین ماده به درون کوره قوس الکتریکی تغذیه می گردد.
کوره قوس الکتریکی (EAF)
EAF برای ساختن فولاد گداخته از DRI به کار می رود.کوره، همراه با سقف آن به یک سو چرخانده می شود، وبا قراضه بار گیری می شود.
قوس جریان الکتریکی توانمندی بین الکترودها و بار کوره به جهش در می آید. این عمل گرمای شدیدی پدید می آورد که بار را ذوب وباعث پیشرفت آن دسته از واکنش های شیمیایی می شود که به تولید فولاد می انجامد.
در پایان فرایند تصفیه ،کارگران جریان برق کوره الکتریکی را قطع می کنند . سپس کوره را کج می کنند ،کوره ای که بر روی اهرم های نوسان کننده ای نصب شده ، تا سرباره بیرون ریزد.
پس از بیرون ریختن سرباره ،کوره ی الکتریکی به سوی دیگر خم می شود . فولاد مایع از دهانه بارگیری خارج می شود ودر پاتیل یا کفچه گرد آوری می گردد.
ریخته گری پیوسته (CC)
فولاد گداخته ی تولید شده در کوره الکتریکی به درون واحد قالب گیری (ریخته گری) وارد می گردد،که آهن گداخته(گدازه)را به شکل شمش در می آورد. فولاد از درون قالبی با شکل ویژه جاری می شود آب سرد به سرعت فولاد را سرد می کند ،و باعثمی شود که به هنگام عبور از میان غلتک های مخصوص سخت شود.
فولاد گداخته تولید شده در کوره ی الکتریکی به درون واحد ریخته گری پیوسته سرازیر می شود که فولاد گداخته را به شمش تبدیل می نماید.
دستگاه نورد
این واحد دیگری است که فولاد گداخته را شکل می دهد . تولید مفتول های فولادی در دستگاه نوردی انجام می گیرد. دستگاه نورد غلتک هایی دارد که طوری شیار یافته اند که بتوانند شمش داغ را به اشکال مقطع گرد، بیضوی، مربع یا شش گوشه در آورند
خواص مکانیکی فولادها :
۱- استحکام مناسب که بین ۴۰۰تا ۲۰۰۰ مگاپاسکال می باشد
۲- قابلیت شکل پذیری بالا
۳- مقاومت خستگی مناسب
۴- مقاومت در درجه حرارت پایین مقاومت در درجه حرارت بالا
۵- قابلیت جوشکاری
دسته بندی فولاد ها :
معمولا به سه دسته فولاد های ساده کربنی فولاد های پر آلیاژی فولاد های کم آلیاژی
انواع فولادهای ساده کربنی :
فولادهای کم کربن – کربن متوسط و پر کربن :
فولاد های کم کربن: که در این فولاد ها مقدار کربن کمتر از ۰.۲% می باشد لذا قابلیت شکل پذیری و فرم دهی بالا دارد که در صنعت بیشتر در مواردی به کار می رود که استحکام پایین همراه با قابلیت انعطاف بالا در نظر باشد
فولاد های کربن متوسط : که در این فولاد ها مقدار کربن بین ۰.۲تا ۰.۵% می باشد که در مقایسه با فولاد کربنی استحکام و سختی بالاتری دارند ولی انعطاف پذیری پایین تری دارند که عموما در صنایع راهسازی و ماشین سازی از این گروه استفاده می شود
فولاد های پرکربن : که در این فولاد ها مقدار کربن پس از ۰.۵% می باشد که افزایش درصد باعث افزایش سختی و کاهش انعطاف پذیری می شود در مواردی استفاده می شود که نیاز به سختی و مقاومت به سایش بالا باشد
فولاد های کم آلیاژی : در این فولاد ها میزان عناصر آلیاژی کمتر از ۸% می باشد . وجود عناصر آلیاژی باعث افزایش خواص مکانیکی فولاد می شود وجود عناصر آلیاژی باعث جلوگیری از تغییر فرم – تابیدگی و ترک خوردن آلیاژ در حین عملیات حرارتی می شود که عمدتا در ساخت قطعات و قالبهای خاص صنعتی ساخته می شود
فولاد های پرآلیاژی : میزان عناصر آلیاژی در این نوع فولادها بیش از ۸% می باشد و در مواردی مصرف می شود که خواص خالی را در نظر داشته باشیم به عنوان مثال مقاومت به خوردگی بالا و مقاومت به سایش بالا و با توجه به اینکه قیمت عناصر بالا می باشد و همچنین تکنولوژی اضافه کردن این عناصر نیز بالاتر می باشد لذا فولاد های آلیاژی از نظر قیمت بالاتر می باشد .
|

06-06-2014
|
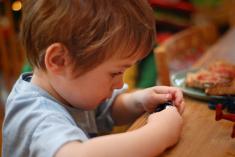 |
مدیر بخش مکانیک - ویندوز و رفع اشکال  
|
|
تاریخ عضویت: Sep 2009
نوشته ها: 2,586
سپاسها: : 5,427
6,159 سپاس در 1,794 نوشته ایشان در یکماه اخیر
|
|
ریخته گری فولاد و تاریخچه آن
انواع کوره های ذوب در فولاد ریزی :
کوره هایی که در ذوب فولاد استفاده می شود شامل کوره های زیمنس مارتین کوره های القایی و قوس کوره های کوپل و کنوتر دوپله کردن کوپل و کنورترمی باشد .
مراحل دوبله کردن کوپل و کنورتر :
۱- تهیه مذاب در کوره کوپل
۲- انتقال به پاتیل با جداره بازی و گوگرد زدائی
۳- تخلیه مذاب در کنورتر به روش اکسیژن و هوا که با دمش هوا کربن سوخته می شود و واکنش های زیررا به وجود می آورد .
Fe+O=FeO
Si+FeO=SiO+Fe+Q
Mn+FeO=MnO+Fe+q
C+FeO=CO+Fe+Q
که کربن لحظه به لحظه می سوزد و مذاب به مذاب فولادتبدیل می شود وجوشش کربن صورت می گیرد لحظه ای که درصد کربن به ۰.۵% در مذاب می رسد فرآیند جوشش کربن به حدی می رسد که فرآیند حرارت را در مذاب نداریم که برای افزایش راندمان به جای هوا اکسیژن تزریق می کنند در روش های جدید برای کنترل بیشتر مذاب مذاب به کورههای القایی منتقل می شود و ترکیب شیمیایی آن کنترل می شود
عملیات کیفی در تهیه قطعات فولادی : شامل اکسیژن زدایی سرباره گیری ریخته گری قطعات تمیزکاری و جوشکاری می باشد .
جهت اکسیژن زدایی در مراحل اولیه از فروسیلیس – سیلیکم منگنز و فرومنگنز استفاده می شود در صورتی که بخواهیم میزان اکسیژن به زیر ۰.۱% برسد از Alو Ti در آخرین مرحله استفاده می شود .
تمیزکاری: معمولا از طریق شات بلاست و سند بلاست انجام می شود
جوشکاری : که بر خلاف چدن در قطعات فولادی به علت قابلیت جوشکاری بالا انجام می شود که شامل پر کردن اثرات انقباضی-گازی و نیامد در کردن در طی فرآیند ریخته گری می باشد
مراحل جوشکاری : انتخاب نوع الکترود و اندازه الکترود عملیات پیش گرم کردن قطعات قبل از جوشکاری عملیات تنش زدایی بعد از جوشکاری تمیز کاری
تست های غیر مخرب : نظیر ماوراء بنفش التراستیگ ایکسرید
تاثیر عناصر جزئی بر فولاد ها ساده کربنی :
منگنز : جزء عناصر موجود در فولاد های ساده کربنی مقدار آن ۰.۶تا ۰.۸۵ درصد که پیش از این مقدار به عنوان عنصر آلیاژی در فولاد ها می باشد باعث افزایش سختی استحکام و مقاومت به ضربه فولاد می شود می تواند به عنوان اکسیژن زدا درفولاد ها استفاده شود .
Si سیلیس : به عنوان اکسیژن زدا استفاده می شود مانع از پایداری سمنتیت می شود مقدار آن ۰.۰۶% می باشد و بیشتر از این مقدار به عنوان عنصر آلیاژی می شود
Niو Cu : تا حدود ۰.۵ باعث افزایش سختی پذیری و خواص مکانیکی می شود که پایدار کننده ی آستینیت می باشد بیشتر از این مقدار به عنوان عنصر آلیاژی محسوب می شود
سایر عناصر آلیاژی نظیر کرم مولیبدن وانادیم و تنگستن تا حدود ۰.۰۵% در فولاد های ساده کربنی وجود دارد که باعث افزایش خواص مکانیکی می شود
Al&TI :به عنوان اکسیژن زدا در مراحل تولید استفاده می شود.
ازت : مقدار آن بین ۰.۰۰۵ تا ۰.۱۲ درصد می باشد تا این مقادیر باعث افزایش خواص مکانیکی می شود بیش از این مقدار به علت تشکیل مک و حفره گازی در قطعات تولیدی باعث کاهش خواص مکانیکی می شود
گوگرد : از عناصر مضر در فولاد می باشد به علت تشکیل فاز FeSتا سولفید آهن که فازی با نقطه ذوب پایین و ترد می باشد و در مراحل انتهایی انجماد در مرز دانه رسوب می کند باعث کاهش شدید خواص مکانیکی می شود همچنین به هنگام عملیات حرارتی به علت ذوب موضعی در مرز دانه باعث ایجاد ترک موسوم به ترک سرخ می شود وجود منگنز تشکیل فاز MnS یا سولفید منگنز را می دهد این فاز نرم بوده و تاثیر سوءکمتری نسبت به FeS دارد MnS در داخل دانه پخش می شود .
فسفر : تمایل به جدایش بیشتری دارد لذا در محل هایی که آخرین انجماد را دارند جمع می شوند تشکیل فاز فسفید آهن یاFe3P را می دهد این فاز تشکیل یوتکتیک سه تایی می دهد که نقطه ذوب پایین دارد که در مرز دانه ها رسوب کرده و باعث شکست دانه ها می شود میزان فسفر و گوگرد کمتر از ۰.۰۵ درصد می باشد
سیستم راهگاهی در فولاد ریزی :
شامل حوضچه بارریز – راهگاه بارریز حوضچه پای راهگاه راهگاه اصلی آشغالگیر کانال های فرعی و اصلی می باشد .
عموما نوع سیستم راهگاهی فشاری بوده s>r>g نکاتی که در طراحی سیستم راهگاهی در فولاد ریزی باید درنظر بگیریم :
بین راهگاه بارریز و حوضچه بارریز شیب زیادی وجود داشته باشد وجود این شیب از نفوذ آخال و هوا به داخل سیستم راهگاهی می شود .
راهگاه بارریز مخروطی می باشد
گوشه های راهگاه اصلی و فرعی گرد می شود
انتهای راهگاه اصلی بعد از آخرین راهگاه فرعی ادامه پیدا می کند تا ناخالصی ها وارد سیستم راهگاهی نشود
در انتهای راهگاه بارریز حوضچه پای راهگاه را در نظر می گیرند
مقطع راهگاه اصلی به طرف راهگاه فرعی کم می شود
حدالامکان از راهگاه اصلی و فرعی عریض استفاده نشود
انجماد جهت دار به طرف تغذیه
جنس راهگاه اصلی در مورد قطعات بزرگ از مواد دیرگداز با نقطه زینتر بالا باشد
تقسیم بندی سیستم راهگاهی بر اساس ابعاد قطعات : عموما چهار نوع راهگاه در فولاد ریزی وجود دارند
۱) راهگاه از بالا برای قطعات با ارتفاع کم
۲) راهگاه از بغل برای قطعات با ارتفاع متوسط وابعاد بزرگ
۳) راهگاه از پایین برای قطعات با ارتفاع بلند در حالت باید فوق ذوب زیاد در نظرگرفته شودتا از انجماد زود رس در سطح مذاب جلوگیری شود
۴) راهگاه پله ای : که برای قطعات با ارتفاع زیاداستفاده می شود هر یک این روش نسبت به روش فوق این است که مذاب در هر لحظه مذاب گرم به سطح مذاب هدایت می شود برای جلوگیری از ورود آخال از راهگاه های مورب استفاده می شود.
تعیین ابعاد سیستم راهگاهی :
نکته : در بین راهگاه اصلی و فرعی معمولا یک آشغال گیر قرار می دهند
تعین ابعاد آشغال گیر:
آشغال گیر و ***** محفظه این دو بین راهگاه اصلی و فرعی می باشد که به منظور آخال گیری و جدا کردن آخال و جلوگیری از ورود آن ها به محفظه قالب تهیه میشود .
کورة القایی
تکنولوژی کورة القایی یک تکنولوژی استراتژیک و پرکاربرد است که از جمله در ذوب فلزات با استفاده از انرژی الکتریکی کاربرد دارد.زیربنای صنایع سنگین هر کشور، صنایع ذوب فلزات است. زیربنای صنایع ذوب نیز صنایع کوره سازی است.لذا از اینجا اهمیت صنایع کورهسازی بوضوح روشن می گردد.
در گذشته بیشتر از کوره های سوخت فسیلی برای ذوب فلزات استفاده می شد . آلودگی محیط زیست، راندمان پایین، سروصدای زیاد، عدم یکنواختی مذاب، عدم توانایی ذوب فلزات دیرگداز و مسائلی از این قبیل، مشکلاتی بود که این کوره ها به همراه داشتند.
در چند دهة اخیر توجه متخصصین و دست اندرکاران کوره سازی به استفاده از انرژی الکتریکیدر این زمینه جلب شد و نسل جدیدی از کوره های الکتریکی بوجود آمد که از این میان به دو مدل از کوره های ذوب می توان اشاره نمود:
۱-کورههای قوس الکتریک
۲- کورههای القایی
کوره های قوس الکتریک برای ذوب فولاد و به منظور فولادسازی مورد استفاده قرار میگیرد که فعلاً بحث دربارة آن مورد نظر نیست. اما دربارة کوره های القایی و یا به عبارتی تکنولوژی گرمایش القایی، زمینة بحث بسیار گسترده و عمیق است که مختصری درباره آن صحبت میکنیم:
تکنولوژی گرمایش القایی در واقع تولید حرارت توسط میدان متغیر مغناطیسی قوی است که توسط سیستمهای مختلفی قابل تولید است.در گذشته این میدانها را توسط ژنراتورهای دینامیکی تولید می کردند. بدین شکل که یک ژنراتور فرکانس متوسط را با یک موتور سه فاز کوپل می کردند و با اضافه کردن یکسری خازن در مدار رزونانس، جریانهای متغیری را در داخل کویل گرمکن بوجود می آوردند. بر این مبنا حرارت در قطعة قرارداده شده در کویل بوجود می آمد.
با پیشرفت تکنولوژی “الکترونیک قدرت” و ساخته شدن سوئیچهای سریع و قوی، نسل جدیدی از ژنراتورها بوجود آمد که اصطلاحاً به آنها ژنراتورهای استاتیکی گفته میشود. در این نوع ژنراتورها حرکت مکانیکی وجود ندارد. بهاضافه اینکه کنترل قدرت ژنراتور بسیار دقیقتر و کاملتر میسر است.
نکتة مهم دیگر اینست که ساخت کورة القایی یک کار تکنولوژیبر است.حداکثر ۲۰ الی ۳۰ درصد قیمت یک کوره, مواد به کار رفته در آن میباشد و بقیه قیمت تکنولوژی آن است. به همین دلیل است که تکنولوژی آن را به ما نمیفروشند. البتهدولت ارزش این تکنولوژی را درک نمیکند و برای وام گرفتن، تنها ملک و زمین را به عنوان وثیقه قبول دارند و تکنولوژی را که ۵۰ میلیون دلار ارزش دارد به عنوان وثیقه قبول ندارند و برای آن ریالی ارزش قائل نیستند.
اهمیت این تکنولوژی در این مطلب نهفته است که زیر بنای بسیاری از تکنولوژیها و صنایع می باشد و به عبارتی اکثر صنایع سنگین به نوعی به این تکنولوژی وابسته اند. مطلب دوم اینکه این تکنولوژی خود بسترساز بسیاری از تکنولوژیهای دیگر است که به نوبة خود برای کشور مفید خواهند بود. با توجه به نیاز کشور به این تکنولوژی به نظر می رسد می باید نظر مسئولین مربوطه نسبت به این صنعت بیشتر جلب گردد تا در آینده بتوانیم شاهد شکوفایی و رشد و ترقی روزافزون این تکنولوژی در کشور باشیم.
|
کاربران در حال دیدن موضوع: 1 نفر (0 عضو و 1 مهمان)
|
|
مجوز های ارسال و ویرایش
|
شما نمیتوانید موضوع جدیدی ارسال کنید
شما امکان ارسال پاسخ را ندارید
شما نمیتوانید فایل پیوست در پست خود ضمیمه کنید
شما نمیتوانید پست های خود را ویرایش کنید
اچ تی ام ال غیر فعال می باشد
|
|
|
اکنون ساعت 11:20 AM برپایه ساعت جهانی (GMT - گرینویچ) +3.5 می باشد.
|